Produktion Neuer Applikationsprozess: Dichten wie gedruckt
Atlas Copco IAS hat ein neues Verfahren entwickelt, bei dem einzelne PVC-Tropfen aufgetragen werden. Das spart Material und verringert die Nacharbeit. Audi setzt die neue Technik bereits für die Abdichtung von Karosserien ein.
Anbieter zum Thema
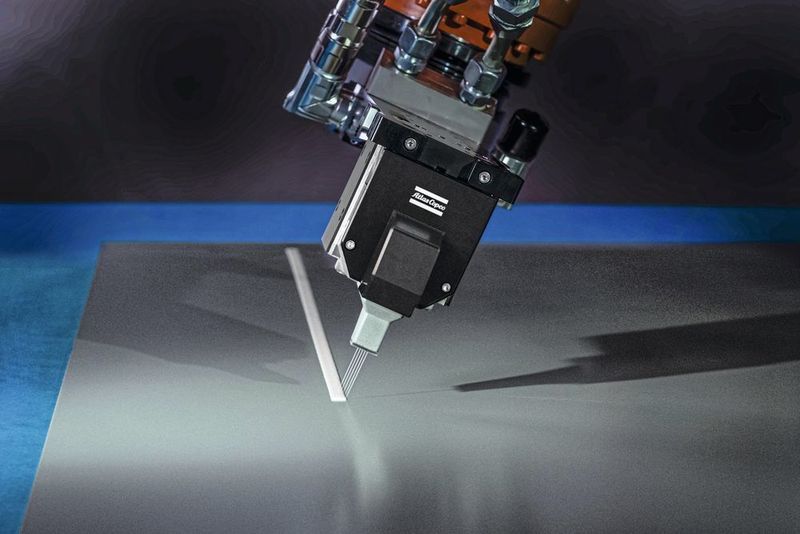
Fragt man Olaf Leonhardt, Geschäftsführer der Atlas Copco IAS GmbH (kurz für Industrial Assembly Solutions), nach dem Prinzip des neuen Verfahrens, vergleicht er „IDDA.Seal“ mit einer Technologie aus der Bürokommunikation: „Stellen Sie sich einfach einen Tintenstrahldrucker vor, der jeden Farbpunkt gezielt setzt.“ Genau so funktioniert auch die „Intelligent Dynamic Drop Application“ (dafür steht die Abkürzung) von Dichtmaterial in Tropfenform. Auf diese Weise werden kosmetische Sichtnähte oder Nahtabdichtungen erzeugt.
:quality(80)/images.vogel.de/vogelonline/bdb/1685500/1685519/original.jpg)
Produktion
Toyota entwickelt fast verlustfreien Lackzerstäuber
Der Applikator am Roboterarm ist mit fünf Nadeldüsen ausgestattet, die individuell konfiguriert und angesteuert werden. So wird das Polyvinylchlorid-Plastisol (= Dispersion aus PVC sowie weiteren Additiven) nicht im konstanten Materialfluss als Raupe, sondern Punkt für Punkt aufgetragen. Dabei lassen sich an jeder Nadel drei Parameter beeinflussen: Öffnen und Schließen, das Tropfenvolumen und die Frequenz, dass heißt der Tropfenabstand.
Flexibler Sprühkopf
Der Unterschied zu den bisherigen Standards für kosmetische Karosserienähte und Nahtabdichtung – das sind Dünnstrahl-, Swirl- und Flatstream-Technologie – ist unmittelbar sichtbar, wenn man die IDDA-Testanlage im Technikum von Atlas Copco IAS im Einsatz sieht. Der vom Roboter geführte und sich mit hohem Tempo bewegende Sprühkopf kann zum Beispiel seine Breite und die Schichtstärke verändern.
Und während die bisherige aufgetragene Raupe nur im rechten Winkel die Richtung wechseln kann, lassen sich mit IDDA Winkel bis +/- 25 Grad darstellen. Auch komplexe Nahtgeometrien mit Einschnürungen, Lücken und Nahtüberlappungen werden ganz selbstverständlich realisiert.
:quality(80)/images.vogel.de/vogelonline/bdb/1671200/1671206/original.jpg)
Oberflächentechnik
Wie moderner Korrosionsschutz funktioniert
Außerdem ist der Winkel, in dem das Material (ziehend oder stechend) aufgetragen wird, nun variabel, so dass der „Spray“ Zonen abdeckt, die zuvor unerreichbar waren. Insgesamt ist die Qualität der Naht deutlich besser, wie Olaf Leonhardt erläutert: „Bei der bisherigen Applikationstechnologie kann es zu Materialanhäufungen an den Wendestellen kommen, oder spitze Winkel werden nicht richtig erreicht.“
Hohe Qualtitä durch hohe kinetische Energie
„Das macht manuelle Nacharbeit erforderlich, um Undichtigkeiten zu vermeiden und überschüssiges Material zu verstreichen“, ergänzt Leonhardt. Wichtig bei Sichtnähten: Die Auftragsqualität ist auch deshalb hoch, weil die einzelnen Tropfen selbst bei geringer Geschwindigkeit mit hoher kinetischer Energie auf den Untergrund auftreffen.
Ein weiterer Vorteil der Applikation „Tropfen für Tropfen“ besteht in der Einsparung von Material und Gewicht. In der Praxis kann sich diese Einsparung auf bis zu 50 Prozent belaufen. Das entspricht mehreren Kilogramm. Der hochpräzise Auftrag mit kontrollierter Schichtdicke kann die manuelle Nacharbeit um bis zu 40 Prozent reduzieren. Das spart Kosten.
Neuer Applikator und schnelle Regelprozesse
Für das neue Verfahren hat Atlas Copco IAS einen neuen Applikator entwickelt und auch eine neue Software, um die extrem schnelle Regelprozesse abzubilden. Dabei haben die Entwickler nicht hinter verschlossenen Labortüren gearbeitet, sondern mit Audi zusammengearbeitet, die folgerichtig der erste Anwender des tropfenweisen PVC-Auftrags ist.
:quality(80):fill(efefef,0)/images.vogel.de/vogelonline/bdb/1680800/1680878/original.jpg)
Vier Jahre hat die gemeinsame Entwicklungsarbeit der Technologie gedauert, die Audi als „Digital Sealing“ bezeichnet. Wie das Kernelement der Innovation – der Applikator – aufgebaut ist, möchte Atlas Copco nicht verraten. Druckluft als Trägermedium scheidet wegen der extrem schnellen und hochgenauen Regel- und Auftragsprozesse wohl aus. Dass es sich um Piezotechnik handeln könnte, wird von den Entwicklern zumindest nicht verneint.
Im Serieneinsatz bei Audi
Audi setzt das Verfahren im Werk Györ in der Karosseriefertigung des Audi Q3 und Q3 Sportback ein – zum Beispiel bei der Nahtabdichtung des Leuchtentopfs und beim Erzeugen der Sichtnaht an der Wasserablaufrinne im Heckbereich. Künftig soll „IDDA.Seal“ an weiteren Audi-Standorten und neben der Feinnahtabdichtung kosmetischer Nähte auch für Grobnahtabdichtungen eingesetzt werden.
Gido Hoppe, als Produktingenieur Lackierte Oberfläche/Korrosionsschutz bei Audi verantwortlich für die Entwicklungspartnerschaft mit Atlas Copco und die Einführung von IDDA-Seal: „Unser Ziel war es, die Applikation des Abdichtungsmaterial deutlich zu vereinfachen, exakter konturierte Dichtnähte und zugleich Gewicht zu sparen. Diese Ziele haben wir erreicht.“
:quality(80)/images.vogel.de/vogelonline/bdb/1670800/1670834/original.jpg)
Automobilzulieferer
„Die klassischen Hebel zur Kostenreduzierung sind weitgehend ausgereizt“
Ein weiteres, ebenfalls erreichtes, Ziel war die Verbesserung der Ergonomie. Denn bislang waren der Automatisierung dieses Verfahrens Grenzen gesetzt, so dass erfahrene Mitarbeiter diese Aufgabe teilweise in Überkopfarbeit am Unterboden erledigen mussten. Jetzt kann der Roboter auch in schlecht zugänglichen Bereichen Dichtnähte setzen.
Die Bezeichnung „IDDA.Seal“ deutet darauf hin, dass es die „Intelligent Dynamic Drop Application“ künftig auch für die Tropfenapplikation anderer Medien geben könnte. Ob das zum Beispiel „IDDA.Glue“ für Kleber oder „IDDA.Coat“ für Beschichtungen sein kann – die Entwickler in Bretten werden es wissen und vielleicht schon daran arbeiten.
(ID:46413472)