HSK im Vergleich Torsionsbruchverhalten von HSK-A und HSK-AB
Anbieter zum Thema
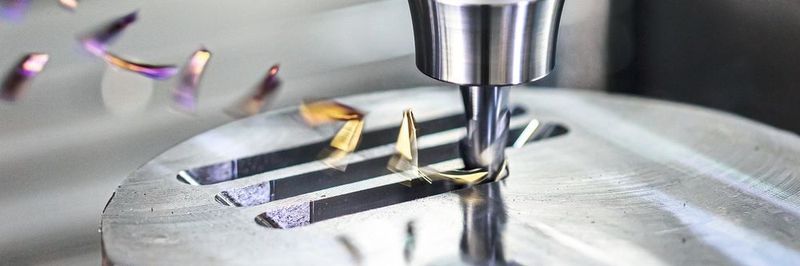
Bearbeitungsaufgaben, die mit hohen Drehzahlen ausgeführt werden, stellen hohe Ansprüche an die Wuchtung der Fräswerkzeuge. Mit der Steigerung der Spindeldrehzahlen steigen die Unwuchtkräfte quadratisch an, sodass kleine Unwuchtmassen bei hohen Drehzahlen zu hohen umlaufenden Kräften und damit zu Vibrationen im Werkzeug führen.
Diese Vibrationen wirken sich gleichermaßen negativ auf die erreichbaren Bauteilqualitäten wie auch auf die Standzeiten der Werkzeuge aus. Insbesondere bei lang auskragenden dünnen Werkzeugen wie Schrumpffuttern wird das dynamische Wuchten in mehreren Ebenen zur Herausforderung, wenn der HSK eine geometriebedingte Unwucht durch die ungleich tiefen Mitnehmernuten aufweist. Diese Unwucht kann im vorderen Bereich des dünnen Werkzeugs kaum ausgeglichen werden.
Eine Lösung für dieses Problem stellt der dynamisch gewuchtete HSK-AB dar, der gemeinsam mit dem HSK-AC und HSK-EB durch die Mitglieder des DIN-Normenausschusses Werkzeuge und Spannzeuge entwickelt und bei der ISO zur Normung vorgeschlagen wurde.
Im Rahmen der Normungsarbeit wurde diskutiert, ob die Wuchtmaßnahmen eine derartige Schwächung des Kegels im Bereich der Mitnehmernuten verursachen, sodass die aus dem VDMA-Einheitsblatt 34181 [1] bekannten Brüche des Nutgrundes bei geringeren Lasten auftreten. Hierzu wurden am WZL der RWTH Aachen University vergleichende Untersuchungen zum Torsionsbruchverhalten des HSK-A und des HSK-AB durchgeführt.
Versuchsmethodik zum statischen Torsionsbruch
Bereits im Zuge der Einführung des HSK wurden Untersuchungen zu den zulässigen Belastungen des HSK durchgeführt mit dem Ziel, die Einsatzgrenzen des HSK zu beschreiben. Unter anderem wurden die Biegebelastbarkeit, Drehzahlgrenzen sowie das statische und dynamische Torsionsbruchmoment untersucht [1, 2]. Aus den gewonnenen Erkenntnissen lässt sich schließen, dass die geometrischen Veränderungen durch die Wuchtmaßnahmen aus Bild 2 lediglich auf das Torsionsbruchverhalten signifikante Auswirkungen haben könnten, da sie im Bereich der flachen Mitnehmernut zu Materialschwächungen und einer Anhäufung von teilweise nicht verrundeten Kanten führen.
Drei verschiedene Werkstoffe wurden untersucht
Da die Versuche aus [1] und [2] bei gleichzeitiger Überlagerung einer Querkraft, eines Biege- und eines Torsionsmoments durchgeführt wurden und überdies keine Erkenntnisse über die Toleranzlagen und die genaue Verarbeitung der Werkzeuge vorliegen, wurde die Durchführung neuer Versuche beschlossen. Bei den Versuchen aus dem VDMA-Einheitsblatt 34181 wurden drei verschiedene Werkstoffe (1.7131, 1.6582, 1.2343) in Baugrößen von 32 bis 125 untersucht. Auch wenn sich die vorgeschlagenen Wuchtmaßnahmen zwischen den Baugrößen minimal unterscheiden, fokussierte man sich bei den aktuellen Untersuchungen auf die Baugröße 63.
Die Versuche wurden mit Werkzeugen aus einsatzgehärtetem 1.7131 (16MnCr5) durchgeführt, was eine vergleichende Abschätzung des Einflusses der Wuchtmaßnahmen auf das Torsionsbruchmoment erlaubt.
Der eingesetzte Statikprüfstand aus Bild 3 erlaubt es, ein Torsionsmoment ohne Überlagerung einer Biegekraft in die Werkzeugschnittstelle einzuleiten. Das Moment wird durch einen hydraulischen Belastungszylinder (1) und einen Hebelarm (3) in eine gelagerte Welle eingeleitet. Durch die Kupplung (4) werden die Welle und das Versuchswerkzeug (8) formschlüssig verbunden. Das Werkzeug wird über einen nicht kraftverstärkenden Spannsatz (11) und eine Zugstange mit DMS-Einzugskraftmessung (12) in den Versuchsflansch eingezogen. Zur Erfassung der Kraft und damit des aufgebrachten Torsionsmoments, kommt ein Kraftsensor (2) zum Einsatz. Der Verdrehwinkel des Werkzeugs relativ zur Aufnahme wird über zwei taktile Wegsensoren (7), welche auf einem Messring (9) auf dem Greiferbund montiert sind, erfasst.
Aus den erfassten Messdaten wird eine Torsionskurve, wie sie in Bild 4 dargestellt ist, erzeugt. Hierzu wird aus den Wegsignalen und dem Abstand der Sensoren der Verdrehwinkel berechnet und über dem Torsionsmoment aufgetragen. Die Kurve zeigt zunächst keine Veränderung des Verdrehwinkels im Bereich der Haftreibung des Werkzeugs.
Bei weiterer Steigerung des Torsionsmoments beginnt das Werkzeug durchzurutschen, bis das Durchrutschmoment überschritten wird und die Kurve einen senkrechten Verlauf annimmt. Darauf folgend bildet sich der Kontakt zwischen den Mitnehmernuten am Werkzeug und den Nutensteinen im Aufnahmeflansch aus, es kommt zu einem Einfedern des Werkzeugs. Wird das Torsionsmoment weiter gesteigert, zeigt ein abrupter Einbruch des Torsionsmoments den Einriss des Mitnehmernutgrunds an. Wird das Torsionsmoment weiter gesteigert, kommt es zu einem weiteren Rissfortschritt, der durch weitere Einbrüche des Torsionsmoments zu erkennen ist.
Ausgewertet wird das Torsionsbruchmoment am Punkt des ersten Einreißens des Mitnehmernutgrundes. Die Höhe des Durchrutschmoments gibt das reibschlüssig übertragene Moment an [3], daher sollte es für alle Versuche ähnlich sein, um eine Vergleichbarkeit der Torsionsbruchmomente zu gewährleisten.
Da der direkte Vergleich der beiden HSK-Formen und im speziellen der Einfluss der Wuchtmaßnahmen an der flachen Nut das Ziel der Untersuchung ist, wurden fünf verschiedene Testszenarien gewählt:
- nur flache Nut am HSK-A,
- nur flache Nut am HSK-AB,
- nur tiefe Nut am HSK-A,
- beide Nuten des HSK-A,
- beide Nuten des HSK-AB.
Hierfür wurden alle HSK-A- und HSK-AB-Werkzeuge aus dem gleichen Material, mit der gleichen Wärmebehandlung und der gleichen Fertigungshistorie hergestellt.
Für jede Versuchsreihe wurde ein neuer Flansch verwendet, in dem je nach Belastungsfall der nicht benötigte Nutenstein entfernt wurde.
Sowohl die Aufnahmen als auch die Werkzeuge wurden auf einem 3D-Koordinatenmessgerät vermessen. Sie liegen in den Normtoleranzen und zeigen keine signifikanten Abweichungen untereinander.
Messergebnisse der Torsionsbruchversuche
Die Ergebnisse der Torsionsbruchversuche sind in Bild 5 zusammengefasst. Abgebildet sind fünf Diagramme mit den jeweils vier bis fünf einzelnen Torsionsbruchkurven der einzelnen Testszenarien sowie die Mittelung der Bruchmomente.
Der Vergleich der Durchrutschmomente aller Versuche zeigt eine gute Übereinstimmung und lässt gleichzeitig mit dem scharfen Übergang aus dem Durchrutschen in das Einfedern auf eine hohe Fertigungsgüte und übereinstimmende Toleranzlage der Werkzeuge bezüglich Kegeldurchmesser und Lage der Nutensteine schließen. Bei Kurven, die kein ausgeprägtes Durchrutschen zeigen (Bild 5: 2. und 5.), ist das Werkzeug bei der Vorbereitung des Prüfstands nach der Montage in Belastungsrichtung an den zu belastenden Nutenstein gerutscht.
Das gemittelte Torsionsbruch- moment des HSK-A (1.) liegt mit 1665,9 Nm leicht über dem des HSK-AB (2.) mit 1435,9 Nm, wobei sich die Konfidenzintervalle nicht schneiden. Die Messkurven zeigen eine gute Übereinstimmung untereinander.
Das um 14 % höhere Bruchmoment des HSK-A im Vergleich zum HSK-AB sollte allerdings nicht als ausschlaggebend gewertet werden, da für die Versuche eine möglichst symmetrische Anlage der Nutensteine angestrebt wurde. Diese kann jedoch in der Praxis aufgrund der erlaubten Toleranzen der Nutensteine und der Mitnehmernuten nicht vorausgesetzt werden. Daher muss für den Vergleich der Veränderungen des Torsionsbruchmoments durch die Wuchtmaßnahmen die Untersuchung der einzelnen Nuten herangezogen werden.
Keine relevanten Veränderungen durch die Wuchtmaßnahmen
Der Vergleich der Torsionsbruchmomente der flachen Nuten von HSK-A (3.) und HSK-AB (4.) mit 987,6 Nm und 1031,8 Nm, wobei sich die Konfidenzintervalle überschneiden, zeigt keine relevante Veränderung durch die Wuchtmaßnahmen. In gleicher Größenordnung liegt das Torsionsbruchmoment der tiefen Nut (5.) mit 964,6 Nm, an der keine Veränderungen durchgeführt wurden. Die Torsionsbruchmomente der drei einzeln untersuchten Nuten unterscheiden sich folglich nicht signifikant.
Die Rissausbreitung an der flachen Nut nimmt beim HSK-AB einen anderen Verlauf, als beim HSK-A. Bild 6 zeigt die Rissausbreitung im Vergleich. Beim HSK-A verläuft der Riss in der Regel entlang der Verrundung des Nutgrundes, läuft senkrecht zur Spannschräge und folgt waagerecht der geringsten Wandstärke. Beim HSK-AB verläuft der Riss ebenfalls zunächst durch die Verrundung des Nutgrundes, läuft dann jedoch in den Grund der Wuchtmaßnahme. Hier folgt der Riss der nicht verrundeten Ecke und verläuft von dort aus ebenfalls zur Spannschräge, danach verläuft er wie beim HSK-A.
Auch wenn die erreichten Torsionsbruchmomente mit beiden Nuten im Eingriff beim HSK-AB geringer sind als beim HSK-A, belegen die Ergebnisse der Untersuchungen der einzelnen Nuten, dass sich die Wuchtmaßnahmen am HSK-AB 63 im Vergleich zum HSK-A 63 nicht negativ auf das statische Torsionsbruchmoment auswirken. MM
Literatur
[1] VDMA 34181: Grenzbelastbarkeit von HSK-Schnittstellen Form A/C gemäß DIN 69893-1 und ISO 12164-1.
[2] Weck, M.; Reinartz, T.: Untersuchungen von Werkzeug und Spannsystemen unter sicherheitstechnischen Gesichtspunkten. Kassel: Verlag Institut für Arbeitswissenschaften Kassel 1999.
[3] Brecher, C.; Müller, F.; Wagner, P.: Werkzeugschnittstellen unter Torsionsbelastung. MM Maschinenmarkt 122 (2016), Nr. 14, S. 64–69. https://www.maschinenmarkt.vogel.de/verhalten-von-werkzeugschnittstellen-unter-torsionsbelastung-a-527636/
* Prof. Dr.-Ing. Christian Brecher ist Inhaber des Lehrstuhls für Werkzeugmaschinen am Werkzeugmaschinenlabor WZL der RWTH Aachen University, Christian Bergs M. Sc. RWTH ist wissenschaftlicher Mitarbeiter und Dr.-Ing. Marcel Fey ist Oberingenieur am WZL in 52074 Aachen. Weitere Informationen: Tel. (02 41) 8 02 62 93, C.Bergs@wzl.rwth-aachen.de
(ID:45804593)