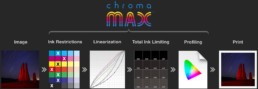
ChromaMax provides guidance for every step of the printer calibration and profiling process
ChromaMax is a calibration methodology that uses color science to achieve maximum saturation, DMax, and gray axis neutrality for optimal image reproduction with minimal ink utilization. Customized bottom weighted targets for each step of the calibration and profiling process allow for greater analysis of deep shadow detail and color. ChromaMax is used to calibrate a wide variety of large format printing processes including aqueous, solvent, latex, UV and dye sublimation. ChromaMax is not used to calibrate a printing process to a standard, but instead, optimizes the full potential of a process for maximum quality. The ChromaMax method is used primarily for demanding, high quality fine art workflows. “Maximum print quality with minimal ink usage” is the mantra of this process.
The ChromaMax method is process and software independant – meaning it can be applied to any printing process through any RIP software.
1. Setup the printer in the RIP using the appropriate multicolor mode instead of a simple color mode like CMYK, when possible.
2. Set the per channel ink restrictions at their chroma peaks. We determine this by printing and measuring the ChromaMax Ink Restrictions target and graphing the chroma. Maximum density and the “more ink is better” approach are depreciated. more…
3. Linearize the printer using curves that define the combined all-color gray axis in Lab color. more…
4. Determine the optimal, combined Total Ink Limit (TIL) that minimizes ink usage without sacrificing shadow color. We determine this by printing and measuring a ChromaMax Total Ink Limit target and graphing the measurements. more…
5. Create an ICC profile that: more…
a) incorporates the perfect TIL in the profile (not the RIP),
b) utilizes a target optimized for that process,
c) utilizes the “sweet spot” black generation curve that minimizes ink usage without sacrificing image quality,
d) is perfectly smooth
e) employs the best perceptual rendering that utilizes a modest amount of chroma darkening to improve the perceptual appearance of edge gamut colors without over saturating mid gamut colors like skin tones.
6. Evaluate.
7. Store final evaluation prints and profiles as references to be used for quality control and repeatability monitoring.
The G7 method is the industry standard linearization procedure that neutralizes the gray axis in Lab color. The G7 method is typically used for calibrating offset presses and proofing devices to achieve offset standards like GRACoL, SWOP and FOGRA.
Maximizing color saturation and black depth (DMax) are priorities for large format and fine art printing. Linearization curves are similar but often contain higher densities, produce more neutral B&W prints, and incorporate the extra “N” channels that fine art processes often utilize.
G7 calls for neutralizing the 100% CMY patch with per ink densities and then performs a Lab neutral gray axis for the combined CMY ramp. G7 assumes the black channel is neutral and linearizes that channel separately for matching L only values. The inks we use in fine art processes are often quite different and the black inks are sometimes surprisingly colorful. For this reason we need a combined all-color Lab linearization that incorporates the colorfulness of the black ink. Fine art processes use ICC profiles so we could care less about neutralizing a 100% CMY patch for example, or lighting to the black to achieve press compliance. Fine are processes aren’t concerned with achieving press specification compliance and are instead, more concerned about maximizing Dmax and saturation, and neutralizing B&W images.
ChromaMax also expands on G7’s linearization-only focus by looking at all the other steps in the process, including ink restrictions, total ink limiting and profiling, all with a focus on perceptual rendering and multichannel support when possible. ChromaMax maximizes color gamut, dmax, gray axis neutrality, and saturation placement all while minimizing ink consumption.
Offset press workflows use common ICC profiles that come with applications like Photoshop. G7 calibrates the press to that press specification so that custom press profiles are not needed and image files don’t go through color space conversations. Fine art workflows utilize custom printer profiles for every single printer/ink/media combination and have different needs for the ‘base calibration’ that’s performed prior to profiling.
G7 and ChromaMax are not in competition with one another. G7 is the right approach for calibrating offset printing presses and achieving a necessary press standard. ChromaMax is the better approach for calibrating and profiling fine art processes.
The ChromaMax method allows printing processes to achieve optimal print quality that appears consistent across a variety of printing processes. This “Maximum print quality with minimal ink usage” approach translates into ink cost savings and reduces problems associated with metamerism. Those involved with fine art reproduction find that they can more easily reproduce original artwork with minimal to no color correction, simplifying a previous tedious task. Shops utilizing this method have a competitive advantage over competitors that do not.
Those that utilize a variety of different printing processes in-house may notice some minor differences between processes. Because the ChromaMax method allows each device to achieve maximum saturation and Dmax, we can visually see the inherent differences between them. For example, a matte paper process might have a light Dmax and gentle color gamut while a dye sub metal process will have incredibly rich blacks and saturation levels. ChromaMax workflows accept these differences as inherent to each process. Aside from these inherent differences, print quality appears extremely consistent across a variety of processes. Soft proofing can be used to simulate these differences only up to a point because display DMax and dark shadow color can be limited, especially on matte surface monitors. ChromaMax calibrated printing processes like dye sublimation often have extreme blacks and saturation levels that even the best displays struggle to reproduce.
The ChromaMax method was developed by Scott Martin of Onsight, starting in 1994 and formalized in 2018. It was created with the idea that optimal print quality could be achieved through repeatable color science instead of sloppy guesswork that was so often utilized during RIP calibration due to the poor tools provided. By analyzing ink restrictions outside of the RIP we could better understand how to set them within the RIP. By creating superior linearization curves outside of the RIP we could import them into the RIP resulting in better tonality that the final ICC Profile wouldn’t struggle to correct. And by precisely calculating the optimal Total Ink Limiting we could achieve optimal shadow color without excessive ink usage. Martin found that with a data driven, color science oriented process he could achieve not only better, but optimal print quality, in less time, with lowered ink consumption on any printer.
The best way to calibrate a printer
Unlock the full potential of your printer
Maximum print quality with Minimal ink usage
Precise color science, not guesswork
Any printer, any RIP
Perfect prints with less ink
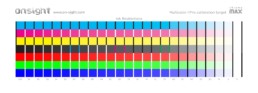
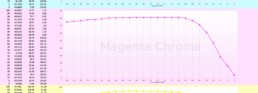
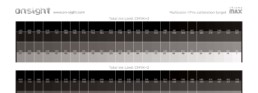
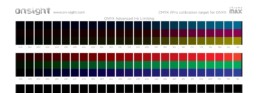
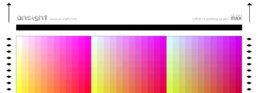