[0001] Die Erfindung betrifft ein Verfahren zur Herstellung von aus wässrigen Färbeflotten
färbbaren, oberflächenmodifizierten Polyolefinfilamentgarnen, die nach diesem Verfahren
erhältlichen Polyolefinfilamentgarne sowie deren Verwendung zur Herstellung von textilen
Flächengebilden.
[0002] Es ist bekannt, dass unmodifiziertes Polypropylen schwer zu färben ist, da es aufgrund
seiner unpolaren Struktur nur schlecht von einer wässrigen Färbeflotte benetzt wird,
wodurch der Übergang des Farbstoffs aus der flüssigen Phase in den polymeren Feststoff
behindert ist. Hinzu kommt, dass der eindiffundierte Farbstoff nur schwache van-der-Waalssche
Wechselwirkungen zum Polymer aufbauen kann.
[0003] Der jährlich weltweit noch immer steigende Bedarf an Textilien aus Polypropylen (PP)
wäre in dieser Form sicherlich nicht festzustellen, wäre es nicht gelungen, das ursprünglich
nicht funktionalisierte, wasserabweisende Faserpolymer zumindest an der Filament-
bzw. Faseroberfläche so zu modifizieren, dass als Folge davon Veredlungs- und Gebrauchseigenschaften
resultieren, die mit Fasern bzw. Filamenten aus anderen polymeren Rohstoffen vergleichbar
sind. Verbesserte Wechselwirkungsmöglichkeiten der PP-Filamentgarne mit ihrer unmittelbaren
- meist wässrigen - Umgebung an deren Oberfläche erlangen aber nicht erst für den
Verbraucher eine kaufentscheidende Bedeutung, sondern sind bereits bei der Herstellung,
Weiterverarbeitung und Veredlung von PP-Filamentgarnen bzw. Textilien von unschätzbarem
Vorteil.
[0004] Aus diesem Grund lag und liegt der Fokus bei der Weiterentwicklung von PP-Filamentgarnen
noch immer auf der Funktionalisierung. Diese erfolgt entweder am polymeren Rohstoff
d.h. am chemischen Grundgerüst und ist damit in der Faser über deren gesamtes Volumen
verteilt. Oder sie wird nur an der Faseroberfläche durchgeführt, was auf die Strukturbildung
in der Faser und die dadurch bedingten mechanisch-physikalischen Eigenschaften im
Gegensatz zur ersteren Variante keinen entscheidenden Einfluss hat. Bezahlt man mit
einer Modifizierung des gesamten Rohstoffs für einen lediglich an der Faseroberfläche
benötigten Effekt im Verhältnis zu viel, so benötigt dem gegenüber eine Modifizierung,
die ausschließlich an der Faseroberfläche durchgeführt wird, in der Regel einen zusätzlichem
Prozessschritt, der natürlich mit entsprechenden Energie- und Anlagekosten verbunden
ist.
[0005] Dieser zusätzliche Prozessschritt wird nach dem heutigen Stand der Technik u.a. dadurch
erreicht, dass durch Einwirkung energiereicher Strahlung im Wesentlichen an der Polymeroberfläche
reaktionsfähige Radikale erzeugt werden. Diese können z.B. mit Sauerstoff oder mit
Sauerstoff enthaltenden Verbindungen, im einfachsten Falle Wasser, reagieren und führen
so zur Bildung von Hydroxygruppen an der PP-Oberfläche. Als Quellen zur Eintragung
der nötigen Strahlungsenergie in das Textil werden dazu heute vielfach UV-, Röntgen-
oder γ-Strahlen sowie Elektronenstrahlen (ß-Strahlung) eingesetzt. Daneben werden
aber auch häufig Behandlungen mit verschiedenen Gas-Plasmen durchgeführt, die je nach
eingesetztem Gas neben Hydroxygruppen auch andere reaktionsfähige funktionelle Gruppen
erzeugen können. Allen Verfahren gemeinsam ist, dass sie in der Regel am fertigen
Textil angewendet werden und dass dafür eine spezielle Anlage zur Strahlen- bzw. Plasmabehandlung
benötigt wird. Dies stellt heute ein zunehmendes Wirtschaftlichkeitsproblem dar, dem
begegnet werden muss, auch wenn unabhängig davon diese Technik in der Lage ist, ein
breites Spektrum interessanter Oberflächeneigenschaften zu erzeugen. Hierzu zählen
beispielsweise die Verbesserung der Benetzbarkeit, der Hydrophilie, der Antistatik,
der Färbbarkeit oder der Haftung an der Polymergrenzfläche. Diese Eigenschaftsverbesserungen
sind daher auch stets Inhalt und Zielrichtung aller Ansätze, die unabhängig von der
angewandten Methode zunächst funktionelle (reaktive) Gruppen auf der PP-Oberfläche
generieren, die dann häufig dazu genutzt werden niedermolekulare Verbindungen oder
Oligomere/Polymere chemisch zu binden bzw. zu pfropfen.
[0006] Die erwähnten unterschiedlichen Ansätze lassen sich nach ihrer verwendeten Methodik
in physikalisch bzw. chemisch initiierte Verfahren einteilen. So werden nach ersterem
z.B. PP-Faser einer UV- oder auch kurzwelligerer Strahlung ausgesetzt, wobei entlang
der Polymerkette Radikale erzeugt werden, die dann in unterschiedlichen Folgereaktionen
unter Bildung polarer, funktioneller Gruppen oder auch leicht flüchtiger, niedermolekularer
Verbindungen abreagieren (
S. Aslanzadeh, M. Haghighat Kish "Photo-oxidation of polypropylene fibers exposed
to short wavelength UV radiations", Fibers and Polymers (2010), 11(5), 710-718). In vielen praktischen Anwendungen wird die Strahlungsbehandlung des Polymers in
Gegenwart von Luft, Singlett-Sauerstoff oder Ozon (
R.L. Clough, K.T. Gillen, "Polymer degradation under ionizing radiation: The role
of ozone", Journal of Polymer Science: Part A-1 27(1989), 2313-2324). durchgeführt, was die Ausbeute an funktionellen Gruppen erhöht, auf der anderen
Seite eine Reaktionskontrolle aber schwieriger macht. Dies kann gerade die kontrollierte
Veränderung der Oberflächeneigenschaften schwierig gestalten. Die spektroskopischen
Methoden (FTIR, NMR, MS), die zur Identifizierung der erzeugten Gruppen eingesetzt
wurden, ergaben, dass Alkohol-, Peroxid-, Keton-, Aldehyd-, Ester-, Perester-, Carbonsäure-
und Anhydridgruppen gebildet werden. Zu den auch mengenmäßig bedeutendsten zählen
die Alkohol-, Peroxid- und Carbonyl-Funktionen, die nicht nur zur Reaktion mit entsprechenden
Veredlungschemikalien genutzt werden können, sondern die sich auch mittels nass-chemischer
Analyse nachweisen lassen (
D. Knittel, E. Schollmeyer, "Functional group analysis on oxidized surfaces of synthetic
textile polymers", Talanta (2008), 76(5), 1136-1140).
[0007] Naturgemäß führt jeder Polymerabbau, auch wenn er nur an der Oberfläche einer Faser
stattfindet, zu strukturellen Veränderungen und zu einem Verlust an mechanischen Eigenschaften
(
EP 1825052, "Gefärbte Polyolefinfasern, deren Verwendung sowie Verfahren zu deren Herstellung").
Das Ausmaß dieser Veränderungen hängt dabei auch von der im Polymer vorhandenen Struktur
ab. So führt die UV-Behandlung eines unorientierten oder wenig orientierten PP-Filamentgarns
in Luft zu einer deutlichen Erniedrigung der Bruchdehnung während ein verstreckter
PP-Faden keine Veränderung zeigt (
Y.J. Hwang, J.S. An, M.G. McCord, S.W. Park, B.C. Kang, "The effect of etching on
low-stress mechanical properties of polypropylene fabrics under helium/oxygen atmospheric
pressure plasma", Fibers and Polymers (2003), 4(4), 145-150). Ein weiteres häufig beobachtetes Phänomen strahlen- und sauerstoffbehandelter PP-Materialien
ist ein Alterungseffekt. D.h. das hergestellte Filamentgarn verliert nach beendeter
Behandlung bei Lagerung zunehmend an Festigkeit. Die Ursache dafür liegt in der unterschiedlichen
Abbaukinetik der verschiedenen in der Behandlung erzeugten Peroxidstrukturen. So wird
das tertiäre Hydroperoxid im Gegensatz zum schnell abbauenden Säureperoxid für den
beobachteten Effekt bei der Lagerung verantwortlich gemacht (
P. Gijsman M. Kroon, M. van Oorschot, "The role of peroxides in the thermooxidative
degradation of polypropylene", Polymer Degradation and Stability (1996), 51(1), 3-13).
[0008] Obwohl die Plasmaentladung eine physikalisch initiierte Methode zur Behandlung von
PP darstellt, kann sie auch als chemisches Verfahren angesehen werden, da die eigentliche
Modifizierung der Polymeroberfläche durch das Gas des Plasmas erfolgt und dadurch
bereits modifiziert wird bevor evtl. anschließend noch eine Umsetzung mit weiteren
reaktiven Verbindungen stattfindet. Die Untersuchungen hierzu sind so zahlreich, dass
nur eine beispielhaft genannt werden soll, um zu verdeutlichen, dass das in diesem
Vorhaben geplante innovative Verfahren zur Oxidation der PP-Oberfläche im Hinblick
auf das Ergebnis natürlich in Konkurrenz zu den etablierten Plasmaverfahren steht.
Auch mit dem Einsatz der Plasmatechnologie soll speziell bei PP als textilem Substrat
wiederum eine Oberflächenmodifizierung erreicht werden, welche eine bessere Benetzbarkeit,
Feuchteaufnahme sowie Färbbarkeit herbeiführt (P. Cocolios, F. Coeuret, F. Forster,
J.-L. Gelot, B. Martens, E. Prinz, G. Rames-Langlade, A. Villermet, "Method for surface
treatment of polymeric substrates",
PCT Int. Appl. (2001), WO 2001058992). Wie erwähnt, wird auch die Plasmabehandlung meist in Kombination mit einer anschließenden
chemischen Reaktion an den erzeugten funktionellen Gruppen genutzt, was aber nicht
zwingend notwendig ist. So ist es beispielsweise möglich, ein PP-Gewebe nach einer
Behandlung mit einem Argon-Plasma und einer anschließenden Umsetzung mit Acrylverbindungen,
Diaminen oder Aminocarbonsäuren mit anionischen oder kationischen Farbstoffen zu färben.
Dies gelingt aber auch schon ohne die beschriebene Umsetzung mit den genannten Verbindungen.
Hier reicht offenbar die aufgrund der hydrophileren Oberfläche verbesserte Benetzbarkeit
bereits aus, die Adsorption des Farbstoffs an der Faseroberfläche und damit die Diffusion
in die Faser zu erleichtern.
[0009] Um gute Hydrophilie zu erreichen, ist eine intensive Plasmabehandlung erforderlich
oder es kommen neue Techniken zur Anwendung, wie die Unterwasser-Plasma-Technik. Dies
ist aber mit einer z.T. deutlichen Veränderung der Fasermorphologie verbunden (Ätzen),
was in Richtung Absorptionsvermögen durchaus gewünscht sein kann, aber auch einen
unerwünscht hohen Effekt auf die mechanischen Eigenschaften haben kann. Um die richtige
Balance zu erreichen, kann man bereits bei der Zusammensetzung der Gasmischung, die
im Plasma zur Anwendung kommt, diesem Effekt Rechnung tragen, indem man ein Gasgemisch
aus einem oxidierenden und einem reduzierenden Gas einsetzt, deren Mischungsverhältnis
wird jeweils auf die Oberflächenspannung des polymeren Substrats abgestimmt.
[0010] Neben den beiden oben beschrieben Möglichkeiten eine Oberflächenmodifizierung der
PP-Faser zu erreichen, ist dies prinzipiell auch durch eine direkte Behandlung mit
geeigneten Chemikalien, in der Regel meist Peroxiden oder Sauerstoff, möglich (
V.E. Caudill, G.W. Halek, "Polypropylene surface characteristics after exposure to
hydrogen peroxide and heat processing" Journal of Plastic Film & Sheeting (1992),
8(2), 140-54). Untersuchungen dazu werden schon recht lange angestellt und betreffen sowohl Reaktionen
in der Gasphase als auch in Lösung, Allen Arbeiten gemeinsam ist das Ergebnis, dass
eine Oxidation des PP nur unter erhöhter Temperatur stattfindet. Die Reaktionen in
der Gasphase verwenden Sauerstoff oder Ozon als Oxidationsmittel, wobei als Substrate
sowohl Fasern als auch Gewebe zum Einsatz kommen (S. Honda, H. Shimizu, "Surface oxidation
of polyolefin fibers with ozone during melt spinning" Jpn. Kokai Tokyo Koho (1973),
JP 48018519). Obwohl für die Behandlung meist Temperaturen von über 100°C angegeben werden, sind
die Behandlungszeiten mit mehreren Minuten im Hinblick auf moderne Produktionsverfahren
sehr lang. Daher werden mitunter auch oxidationsfördernde Agentien, wie z.B. Metallsalze
(
D.E. Bergbreiter, N. White, J. Zhou, "Modification of polyolefin surfaces with iron
cluster oxidants" Journal of Polymer Science, Part A: Polymer Chemistry (1992), 30(3),
389-96) auf das polymere Substrat aufgebracht, welche die Oxidationsausbeute erhöhen sollen.
[0011] Eine erste Beschreibung der Behandlung von Spinnfasern mit Ozon bzw. einer Ozon-Luft-Mischung
findet sich in den 60er und 70er Jahren in Patentanmeldungen. Hierin wird eine zehnminütige
Einwirkung auf einen 100°C heißen Faden beschrieben (M. Lazar, J. Pavlinec, D. Berek,
Z. Manasek, M. Micko, "Oxidation of polypropylene to accumulate peroxide and hydro-peroxide
functional groups", (1963),
CS 106425, Application:
CS 19610313) und/oder eine Einwirkung während des Verstreckprozesses (F. Geleji, G. Odor, "Modified
polypropylene fiber", (1964),
HU 151336). Die mechanische Festigkeit der Fasern soll bei ersterem Verfahren nur wenig abfallen.
[0012] In den bekannt gewordenen Versuchen die Oxidation einer PP-Oberfläche über die flüssige
Phase zu erreichen, werden meist Wasserstoffperoxid oder organische Peroxide eingesetzt
(
C. Marco, C. Blancas, "Degradation of isotactic polypropylene in solution with organic
peroxide" Revista de Plasticos Modernos (2002), 84(554), 176-184; CAN 138:288070). Auch dabei wird die Reaktion durch erhöhte Temperatur unterstützt,
aufgrund der wässrigen Systeme liegen diese aber unter 100°C. Obwohl sich dabei u.U.
ATR-FTIR-spektroskopisch kein Sauerstoff auf der PP-Oberfläche nachweisen lässt, zeigen
Kontaktwinkelmessungen und elektronenmikroskopische Aufnahmen eine Veränderung an.
Wird die Oxidation mit Wasserstoffperoxid in einem organischen Lösungsmittel durchgeführt
und gleichzeitig das entstehende Wasser entfernt, so kann der Prozess verbessert und
auf eine Vielzahl von organischen Substraten angewendet werden (M. Emsenhuber, G.
Kwant, K. Van Straaten, M. Janssen, P. Alsters, H. Hoving, "Process for singlet oxygen
oxidation of organic substrates", Eur. Pat. Appl. (2004),
EP 1403234 A2).
[0013] Ausgehend von dem vorstehend geschilderten Stand der Technik liegt der Erfindung
die komplexe Aufgabe zugrunde, das eingangs beschriebene Verfahren so weiterzubilden,
dass die bekannte Nachbehandlung von Textilien mittels Plasmabehandlung, welche momentan
den Stand der Technik ausmacht, nicht mehr notwendig ist. Vielmehr soll die Erfindung
"inline", d.h. im Schmelzspinnprozess, eine geeignete Behandlung mit dem Ergebnis
vorschlagen, dass die Filamentgarne bzw. die daraus hergestellten Textilien vorteilhaft
mit Küpenfarben, insbesondere nach einem Standardfärbeverfahren, gefärbt werden können
und dass hohe Gebrauchsechtheiten, insbesondere hohe Lichtechtheiten, erhalten werden.
[0014] Erfindungsgemäß wird die oben beschriebene Aufgabe durch ein Verfahren zur Herstellung
von aus wässrigen Färbeflotten färbbaren, oberflächenmodifizierten Polyolefinfilamentgarnen
gelöst, das dadurch gekennzeichnet ist, dass Polyolefinfilamentgarne auf Basis von
Homo- und/oder Copolymerisaten von Propylen und/oder Ethylen, gegebenenfalls mit einem
oder mehreren Comonomeren, während der Fadenbildung im Schmelzspinnprozess zur Hydrophilisierung
der Oberfläche unterhalb des Schmelzpunktes der Polyolefinmaterialien mit einer Wasserstoffperoxidlösung,
insbesondere mit einer wässrigen Wasserstoffperoxidlösung, behandelt werden. Die Oberflächenbehandlung
mit Wasserstoffperoxid erfolgt unterhalb des jeweiligen Schmelzpunktes des Filamentgarnmaterials.
Würde diese oberhalb des Schmelzpunktes, demzufolge bei flüssigem Zustand des Materials,
erfolgen, würden die Filamentgarne bzw. Fäden zerstört werden. Auch darf der Faden
nicht weitgehend abgekühlt werden. Ein nachträgliches Erwärmen und Behandeln mit Wasserstoffperoxid
würde nicht zu dem gewünschten Erfolg führen.
[0015] Es ist bevorzugt, dass eine wässrige Wasserstoffperoxidlösung eingesetzt wird, deren
Konzentration an Wasserstoffperoxid weniger als etwa 35 Gew.-%, insbesondere etwa
0,5 bis 35 Gew.-%, beträgt. Besonders bevorzugt ist es, wenn die Konzentration der
wässrigen Wasserstoffperoxidlösung an Wasserstoffperoxid bei etwa 1 bis 30 Gew.-%,
insbesondere 1,5 bis 10 Gew.-%, liegt.
[0016] Für das erfindungsgemäße Verfahren ist es wesentlich, dass die Behandlung der Oberfläche
der Polyolefinfilamentgarne mit einer Wasserstoffperoxidlösung erfolgt. Dabei gilt
es als besonders bevorzugt, wenn diese Behandlung im Blasschacht der Spinneinrichtung
unterhalb der Spinndüse mittels eines Präparationsstiftes mit Zwangsdosierung durchgeführt
wird. Es handelt sich hier zweckmäßigerweise um eine Präparationseinrichtung bzw.
einen Präparationsstift, der üblicherweise zum Spin finishing herangezogen wird. Die
angesprochene Zwangsdosierung ist deswegen zweckmäßig, um einen gleichmäßigen Oberflächenauftrag
der Wasserstoffperoxidlösung mit der Folge zu erzielen, dass die spätere angestrebte
Färbung gleichmäßig erscheint. Wenn im Übrigen die Auftragseinrichtung, mit der Wasserstoffperoxid
erfindungsgemäß eingebracht wird, insbesondere mit dem Präparationsstift, zu nahe
an der Spinndüse liegt, dann führt dies, wenn der Faden noch flüssig ist, zu einem
Verkleben in der Auftragseinrichtung bzw. dem Präparationsstift. Damit wird der erfindungsgemäße
Rahmen verlassen. Somit lässt sich nun fachmännisch und einfach ermitteln, wann frühestens
mit der Behandlung mit Wasserstoffperoxidlösung im erfindungsgemäßen Verfahren begonnen
werden kann. Der weitere Parameter, wie weit man von der Düse Abstand nehmen sollte,
könnte beispielsweise auch dadurch ermittelt werden, indem bei einem späteren Test
der Färbbarkeit ermittelt wird. Ist die Färbbarkeit schlecht, dann muss der Auftrag
der Wasserstoffperoxidlösung auf die Fäden bzw. das Filamentgarn in einem geringeren
Abstand zur Spinndüse vorgenommen werden. Eine Temperaturangabe ist hier nicht möglich
bzw. reproduzierbar. Der Faden reißt aufgrund seiner hohen Geschwindigkeit noch Luft
mit sich, so dass letztlich mit beispielsweise einer Wärmebildkamera der Faden nicht
als solcher vermessen wird, sondern die Luftumhüllung des Fadens.
[0017] Es hat sich dabei als besonders zweckmäßig erwiesen, dass der Applikationsabstand
(zwischen Spinndüse und Applikationsstelle) der Wasserstoffperoxidlösung im Blasschacht
weniger als etwa 4 m, insbesondere weniger als etwa 2 m beträgt. Ganz besonders wird
es bevorzugt, wenn der Applikationsabstand bis zu etwa 1,5 m beträgt. Um die gestellte
Aufgabe in wünschenswertem Umfang zu lösen, ist es zweckmäßig, der Menge an aufgebrachtem
(reinem) Wasserstoffperoxid Aufmerksamkeit zuzuwenden. Dabei gilt es als vorteilhaft,
wenn die Menge an aufgebrachtem (reinem) Wasserstoffperoxid, bezogen auf das Filamentgarngewicht,
auf bis zu etwa 10 Gew.-%, insbesondere auf mehr als etwa 0,1 Gew.-%, eingestellt
wird. Besonders bevorzugt ist es, wenn die Menge an aufgebrachtem (reinem) Wasserstoffperoxid,
bezogen auf das Filamentgarngewicht, auf etwa 0,2 bis 2 Gew.-% eingestellt wird. Im
Übrigen ist die Temperatur der eingesetzten Wasserstoffperoxidlösung nicht kritisch.
So kann sie beispielsweise Raumtemperatur aufweisen. Ein Erwärmen gibt keinen Sinn,
da letztlich für die Wirkung des Wasserstoffperoxids im Sinne der Erfindung die Temperatur
auf der Oberfläche der Filamente bestimmend ist.
[0018] Zur Optimierung des erfindungsgemäßen Verfahrens ist es sinnvoll, die Filamentgarne
unter der Spinndüse mit einer Geschwindigkeit zwischen etwa 300 und 3000 m/min, insbesondere
zwischen etwa 750 und 2700 m/min, abzuziehen und danach zu verstrecken.
[0019] Im Rahmen der Erfindung und bei sämtlichen vorstehend bezeichneten Ausgestaltungen
ist es darüber hinaus vorteilhaft, wenn das erfindungsgemäße Verfahren, insbesondere
über den Polymerdurchsatz im vorgeschalteten Extruder, so gesteuert wird, dass der
Filamenttiter der hergestellten Filamentgarne auf 0,1 dtex bis 20 dtex eingestellt
wird. Dabei erfolgt die Einstellung des Filamenttiters vorzugsweise derartig, dass
bei der späteren Anwendung der Filamentgarne in Teppichen der Filamenttiter zwischen
etwa 10 und 20 dtex, in Kleidung zwischen etwa 1 und 5 dtex und in Textilien auf Basis
von Mikrofasern weniger als etwa 1 dtex, insbesondere etwa 0,1 bis 0,8 dtex, beträgt.
[0020] Zu den Ausgangsmaterialien ist noch Folgendes auszuführen: Besonders bevorzugt ist
das erfindungsgemäße Verfahren auf Polyolefinfilamentgarne anzuwenden, bei denen es
sich um Homopolymerisate des Propylens (PP) handelt. Hierbei sind insbesondere solche
Homopolymerisate des Polypropylens von Bedeutung, deren Schmelzflussrate MFR [g/10
min], gemessen nach ISO1133, bei 230°C und 2,16 kg Belastung, zwischen etwa 1 und
600, insbesondere zwischen etwa 10 und 45, liegt. Als ein für die Verarbeitung geeigneter
vorteilhafter Rahmen für die Temperatur der Polymerschmelze (PP) kann hier ein Bereich
von etwa 230 bis 270°C, insbesondere von 235 bis 265°C, definiert werden.
[0021] Von Vorteil sind im Rahmen der Erfindung als Ausgangsmaterial auch Homopolymerisate
des Ethylens. Für dieses gelten als bevorzugte MFR-Werte [g/10 min], gemessen bei
190°C und 2,16 kg Belastung, etwa 0,5 bis 150, insbesondere etwa 5 bis 20.
[0022] Auch Copolymerisate von Propylen sowie Ethylen mit mindestens einem weiteren Comonomer
sind für die Zwecke der Erfindung bedeutsam. Bei der Herstellung des Copolymerisats
wird hier zweckmäßigerweise neben Propylen bzw. Ethylen mindestens ein weiteres Comonomer
mit einer olefinischen Doppelbindung eingesetzt. Hierbei kann es sich beispielsweise
um: Vinylacetat, Butadien, cyclische Olefine und dergleichen handeln.
[0023] Gegebenenfalls können die erfindungsgemäß eingesetzten Polymere oder Copolymere,
die auf Propylen und/oder Ethylen zurückgehen, ein oder mehrere weitere Polymere oder
Copolymere enthalten. Hierbei kann es sich beispielsweise handeln um: chemisch gleiche
Polymere des Propylens oder Ethylens oder Copolymere hiervon aber mit unterschiedlichem
Molekulargewicht oder um chemisch verschiedene Polymere oder Copolymere. Der Anteil
an diesen weiteren Komponenten unterliegt in diesen Polymermischungen zweckmäßigerweise
folgenden Rahmenbedingungen: ihre Mischungsanteile sind für jede einzelne Komponente
stets geringer als der des Ausgangspolymers oder -copolymers.
[0024] Gegenstand der vorliegenden Erfindung sind auch nach dem oben beschriebenen erfindungsgemäßen
Verfahren erhältliche Polyolefinfilamentgarne. Es hat sich gezeigt, dass die erfindungsgemäßen
Polyolefinfilamentgarne in guter Übereinstimmung mit der Aufgabe, von der die Erfindung
ausgeht, stehen. So zeigen sie eine Farbtiefe, angegeben als K/S-Wert, die mindestens
doppelt so groß wie der entsprechende Wert ist, der mit einer nicht mit Wasserstoffperoxid
behandelten Probe erreicht wird. Damit wird eine Farbtiefe erzielt, die mit den Handelsprodukten,
wie nachfolgend gezeigt, vergleichbar ist bzw. höher liegt. Dies ist mit dem besonderen
Vorteil der Erfindung verbunden, dass keine nachteilige Nachbehandlung der Polyolefinfilamentgarne
entsprechend dem Stand der Technik mit einer aufwändigen Plasmabehandlung verbunden
ist.
[0025] Durch diese besondere Färbbarkeit der erfindungsgemäß erhältlichen Polyolefine werden
diese vorteilhaften Verwendungsmöglichkeiten zugänglich. So ist Gegenstand der Erfindung
auch die Verwendung der erfindungsgemäßen Polyolefinfilamentgarne zur Herstellung
von textilen Flächengebilden, insbesondere von Gestricken, Geweben, Vliesen und Gewirken,
wobei sich deren vorteilhafte Eigenschaften insbesondere darin erweisen, dass ein
vorteilhaftes anschließendes Färben mit Küpenfarbstoffen erfolgen kann. Es ist besonders
bevorzugt, wenn die Färbung der erfindungsgemäß erhaltenen textilen Flächengebilde
mit üblichen Küpenfarbstoffen, insbesondere nach dem Thermosolverfahren, aus einer
wässrigen Färbeflotte vorgenommen wird.
[0026] Die Erfindung soll nachfolgend noch näher erläutert werden, dies insbesondere im
Hinblick auf technologische Gesichtspunkte: Für die Erfindung reicht es demzufolge,
ohne eine Veränderung am gesamten polymeren Ausgangsmaterial vorzunehmen zu müssen,
ausschließlich die bei der Fadenbildung im Schmelzspinnprozess erzeugte Faseroberfläche
nass-chemisch in der beschriebenen Weise zu modifizieren und damit die Bulkphase,
sprich das Faserinnere, unverändert zu lassen. Die hierfür vorgesehene Behandlung
erfolgt demzufolge erfindungsgemäß "inline", d.h. im Schmelzspinnprozess kurz unterhalb
der Spinndüse, dies mit einer Wasserstoffperoxidlösung, wobei eine partielle Oxidation
an der Faseroberfläche und die Erzeugung funktioneller Gruppen mit u.a. hydrophilen
Eigenschaften erreicht wird. Dadurch kann auf einen separaten Prozessschritt verzichtet
werden, wie er üblicherweise im späteren Verlauf der Verarbeitungskette nach dem Stand
der Technik benötigt wird (z.B. Plasmabehandlung), um einen vergleichbaren Effekt
zu erzielen.
[0027] Der oben beschriebene erfindungsgemäße Ansatz ist bisher nicht beschrieben und unterscheidet
sich damit prinzipiell von einem Nachbehandlungsverfahren mittels Plasmabehandlung
von Textilien, welches momentan den Stand der Technik ausmacht. Demgegenüber führt
der erfindungsgemäße peroxidische Abbau der Homo- und Copolymeren der vorstehend beschriebenen
Art durch Reaktivextrusion, der in der industriellen Praxis primär auch dazu genutzt
wird, um ein besser verarbeitbares Polymer mit kontrollierter Rheologie zu erzeugen,
zwar auch dazu, dass sich die gebildeten funktionellen, sauerstoffhaltigen Gruppen
nach der Fadenbildung nicht nur im Filament-Inneren, sondern, eine homogene Verteilung
vorausgesetzt, auch an der Filamentoberfläche wiederfinden. Die resultierende Oberflächenkonzentration
ist jedoch vergleichsweise minimal, so dass keine merklichen Veränderungen der Grenzflächeneigenschaften
zu verzeichnen sind. Wollte man mittels peroxidischem Abbau eine wirksame Funktionalisierung
der Filamentoberfläche erreichen, so müsste das Ausgangshomo- oder -copolymer so stark
abgebaut werden, dass die nötigen mechanischen Eigenschaften und die Spinnbarkeit
nicht mehr gegeben wären. Aus diesem Grund kann der peroxidische Abbau und jede andere
Art der Bulkmodifizierung nicht als echte Alternative zu einer Oberflächenbehandlung
der beschriebenen Filamentgarne angesehen werden.
[0028] Unter diesem Gesichtspunkt ist die Anwendung der zu Beginn genannten und vom Verfahren
her völlig neuen Art der Modifizierung der Filamentoberfläche - wie sie in dieser
Erfindung beschrieben wird - besonders vorteilhaft, da die immanente Reaktionsfähigkeit
des noch heißen sich bildenden Fadens unter der Spinndüse dazu genutzt wird, durch
Reaktion mit dem kostengünstigen Oxidationsmittel die Funktionalisierung herbeizuführen.
Als Nebenprodukt wird dabei lediglich Wasser gebildet, was dieses Verfahren auch aus
ökologischen Gründen reizvoll macht.
[0029] Erfindungsgemäß spielen bei der Realisierung des hier beschriebenen Verfahrens zwei
Teilaspekte eine gleichrangige Rolle: die Chemie der Modifizierung und die Position
im Prozessablauf, an der die Modifizierung stattfinden muss. Beide sind im Schmelzspinnprozess
notwendigerweise miteinander verbunden, denn die Position bestimmt die Reaktions-
d.h. die Fadentemperatur, die an der Applikationsstelle zur chemischen Modifizierung
der Filamentoberfläche ausgenutzt wird, und damit die Reaktivität und den Umsatz.
Im Hinblick auf den ersten Aspekt erfolgt wie bei vielen der heute angewandten Verfahren
die chemische Modifizierung der Filamentoberfläche, insbesondere der PP-Filamentoberfläche,
über eine Oxidation der Filament-/Polymeroberfläche. Entscheidend dafür und damit
grundsätzlich verschieden von den angewandten Verfahren ist dabei aber, dass diese
Oxidationsreaktion im vorliegenden Verfahren einzig und allein mit verdünnter Wasserstoffperoxid-Lösung
(H
2O
2) erfolgt. Normalerweise reicht diese Randbedingung allein für eine Oxidation der
Textiloberfläche, insbesondere der PP-Textiloberfläche, in der Praxis nicht aus, weshalb
üblicherweise der Einsatz eines Initiators in Form von Strahlungs- oder thermischer
Energie oder in Form eines Radikalbildners notwendig wird. Erst so ist man bislang
in der Lage eine Radikalstelle beispielsweise in der PP-Kette zu erzeugen, welche
dann zur gewünschten Funktionalität (Hydroxygruppe, Carbonylgruppe etc.) abreagieren
kann.
[0030] Bei der Durchführung des erfindungsgemäßen Verfahrens hat sich nun überraschenderweise
gezeigt, dass eine Initiierung bereits dadurch erreicht werden kann, dass man den
Behandlungsschritt vom Stadium der Textilveredlung in das Stadium der Fadenbildung
beim Schmelzspinnprozess vorverlegt. Unter den dort vorherrschenden Bedingungen und
den sich im und am Faden bildenden Strukturen, die von den Prozessvariablen geprägt
sind, wird dabei die angestrebte Funktionalisierung der Filamentoberfläche erreicht,
welche dann die Realisierung der für die Weiterverarbeitung und Anwendung wichtigen
Eigenschaften und Effekte der Filamentgarne ermöglicht.
[0031] Als wichtige physikalisch-chemische Eigenschaften treten dabei an den Filamentgarnen
u.a. Veränderungen des Feuchteaufnahmevermögens, der Fadenreibungskoeffizienten sowie
der fadenmechanischen Daten auf, während am textilen Flächengebilde außerdem Veränderungen
des Oberflächenwiderstands und des Färbeverhaltens zu verzeichnen sind. Gerade beim
Färbeverhalten mit Küpenfarbstoffen werden erfindungsgemäß sehr gute Effekte hinsichtlich
der Farbstoffaufnahme beobachtet.
[0032] Die Durchführung des erfindungsgemäßen Verfahrens eröffnet eine neuartige Möglichkeit,
die Modifizierung von Polyolefinfilamentgarnen, insbesondere PP-Filamentgarnen, während
des Herstellungsprozesses in die existierende Produktionstechnik zu integrieren, ohne
dass dazu eine grundsätzliche Änderung am Aufbau der Produktionsanlage oder an den
Einstellungen der Produktionsparameter notwendig ist. Dies stellt eine bisher nicht
bekannte Neuerung dar, bei der gegenüber der bisherigen Praxis lediglich im bzw. nach
dem Blasschacht bis etwa vier Meter unterhalb der Spinndüse, d.h. dort wo üblicherweise
die Spinnpräparation aufgetragen wird, eine verdünnte H
2O
2-Lösung auf das Filamentbündel appliziert wird. Die an dieser Stelle noch heiße Oberfläche
der Filamente wird durch den angreifenden Sauerstoff des Wasserstoffperoxids ohne
weitere Initiierung direkt oxidiert und die angegriffene Stelle in der Polymerkette
reagiert zur Hydroxygruppe weiter. Dadurch steigen die Hydrophilie und die Benetzbarkeit
der Polyolefinfilamentgarne, insbesondere der PP-Filamentgarne, außerdem werden alle
damit zusammenhängenden Eigenschaften verbessert. In welchem Ausmaß dies geschieht
ist neben der H
2O
2-Konzentration von den verschiedenen Variablen im Extrusionsprozess abhängig. Die
wichtigsten Variablen sind dabei die Verarbeitungs-/Schmelzetemperatur, der Filamenttiter,
die Applikationshöhe (Abstand zur Schmelzspinndüse) und die Anblasung sowie die Abzugsgeschwindigkeit
unter der Düse. Die Applikation des Wasserstoffperoxids erfolgt über einen Präparationsstift
(auch als Präparationsdüse bezeichnet) mit Zwangsdosierung wie sie üblicherweise zur
Auftragung von Spinfinishes in Schmelzspinnprozessen verwendet wird. Die Vorrichtung
zum Auftrag des Spinfinish ist ein unverzichtbarer Bestandteil der Extrusionsanlage,
so wie er in jeder produktionsüblichen Anlage zum Einsatz kommt, und besteht aus einer
Keramikdüse, die von einer Präzisionszahnradpumpe mit der zu applizierenden Flüssigkeit
aus einem Vorratstank heraus versorgt wird. Diese Flüssigkeiten sind Lösungen, Emulsionen
oder reine Spinfinishöle; in der vorliegenden Erfindung sind dies Wasserstoffperoxidlösungen.
[0033] Die Extrusions- und Wickelbedingungen bei der Filamentgarnherstellung liegen im Rahmen
der üblichen Werte für die Produktion von LOY, POY- bzw. FDY-Materialien aus Polypropylen.
Als besonders günstig haben sich dabei erwiesen: Massetemperaturen in der Extrusionsspinnanlage
im Bereich von etwa 220°C bis 290°C und/oder Düsenlochzahlen von etwa 10 bis 100 Loch
und/oder Abzugsgeschwindigkeiten von etwa 300 m/min bis 3000 m/min. Mit diesen werden
vorzugsweise Filamenttiter von etwa 0,1 dtex bis 20 dtex ersponnen, wobei die erzielten
Reißfestigkeiten im Bereich von bis zu etwa 60 cN/tex liegen. Die erfindungsgemäßen
Filamentgarne können unter üblichen Bedingungen zu textilen Flächengebilden, vorzugsweise
Gestricken, weiterverarbeitet werden.
[0034] Wie vorstehend bereits dargestellt, ist ein weiterer Gegenstand der vorliegenden
Erfindung die Verwendung der erhaltenen Polyolefinfilamentgarne, insbesondere Polypropylenfilamentgarne,
und der daraus erhältlichen Flächengebilde zu einem vorteilhaften Färben. Dabei können
die erfindungsgemäßen Polyolefinfilamentgarne bzw. die daraus erhaltenen Flächengebilde
nun in einfacher Weise nach einem Standardverfahren aus wässriger Färbeflotte gefärbt
werden. Dies wird anhand von Küpenfärbungen erreicht, die nach einem Thermosolverfahren
durchgeführt werden und die im erfindungsmäßen Verfahren hohe Gebrauchsechtheiten,
insbesondere Lichtechtheiten aufweisen.
[0035] Nachfolgend wird die Erfindung anhand von Beispielen noch näher erläutert.
Beispiel 1
[0036] Kommerzielles Polypropylengranulat von Lyondell/Basell mit der Bezeichnung Moplen
HP561R (MFR[230°C/2,16kg] 25 g/10min nach ISO 1133) wird der Extrusionsspinnanlage
zugeführt und bei einer Massetemperatur von 260°C zu einem LOY-Filamentgarn mit 24
Filamenten und einem Filamentgarntiter von 90 dtex versponnen. Die Konzentration der
verwendeten Wasserstoffperoxidlösung betrug 3,5%. Die auf den Filamentgarntiter bezogene,
aufgetragene Wasserstoffperoxidmenge betrug 0,77%, wobei in einem Abstand von 1,2m
unter der Spinndüse appliziert und das Filamentgarn mit einer Abzugsgeschwindigkeit
von 1000 m/min produziert wurde.
Beispiel 2
[0037] Kommerzielles Polypropylengranulat von Lyondell/Basell mit der Bezeichnung Moplen
HP561R (MFR[230°C/2,16kg] 25 g/10min nach ISO 1133) wird der Extrusionsspinnanlage
zugeführt und bei einer Massetemperatur von 260°C zu einem LOY-Filamentgarn mit 24
Filamenten und einem Filamentgarntiter von 90 dtex versponnen. Die Konzentration der
verwendeten Wasserstoffperoxidlösung betrug 35%. Die auf den Filamentgarntiter bezogene,
aufgetragene Wasserstoffperoxidmenge betrug 7,7%, wobei in einem Abstand von 1,2m
unter der Spinndüse appliziert und das Filamentgarn mit einer Abzugsgeschwindigkeit
von 1000 m/min produziert wurde.
Beispiel 3
[0038] Kommerzielles Polypropylengranulat von Lyondell/Basell mit der Bezeichnung Moplen
HP561R (MFR[230°C/2,16kg] 25 g/10min nach ISO 1133) wird der Extrusionsspinnanlage
zugeführt und bei einer Massetemperatur von 260°C zu einem POY-Filamentgarn mit 24
Filamenten und einem Filamentgarntiter von 120 dtex versponnen. Die Konzentration
der verwendeten Wasserstoffperoxidlösung betrug 3,5%. Die auf den Filamentgarntiter
bezogene, aufgetragene Wasserstoffperoxidmenge betrug 0,35%, wobei in einem Abstand
von 1,2m unter der Spinndüse appliziert und das Filamentgarn mit einer Abzugsgeschwindigkeit
von 2500 m/min produziert wurde.
Beispiel 4
[0039] Kommerzielles Polypropylengranulat von Lyondell/Basell mit der Bezeichnung Moplen
HP561S (MFR[230°C/2,16kg] 33 g/10min nach ISO 1133) wird der Extrusionsspinnanlage
zugeführt und bei einer Massetemperatur von 240°C zu einem FDY-Filamentgarn mit 24
Filamenten und einem Filamentgarntiter von 100 dtex versponnen. Die Konzentration
der verwendeten Wasserstoffperoxidlösung betrug 3,5%. Die auf den Filamentgarntiter
bezogene, aufgetragene Wasserstoffperoxidmenge betrug 1,45%, wobei in einem Abstand
von 1,2m unter der Spinndüse appliziert und das Filamentgarn mit einer Abliefergeschwindigkeit
von 2800 m/min produziert wurde.
Beispiel 5 bis 8
[0040] Kommerzielles Polypropylengranulat von Lyondell/Basell mit der Bezeichnung Moplen
HP561S (MFR[230°C/2,16kg] 33 g/10min nach ISO 1133) wird der Extrusionsspinnanlage
zugeführt und bei einer Massetemperatur von 260°C zu einem POY-Filamentgarn mit 32
Filamenten und einem Filamentgarntiter von 120 dtex versponnen. Die Konzentration
der verwendeten Wasserstoffperoxidlösung betrug 3,5%. Die auf den Filamentgarntiter
bezogene, aufgetragene Wasserstoffperoxidmenge betrug 0,35%, wobei in einem Abstand
von 1,1m, 1,2m, 1,35m und 1,45m unter der Spinndüse appliziert und das Filamentgarn
mit einer Abzugsgeschwindigkeit von 2500 m/min produziert wurde.
[0041] Die wichtigsten Herstellungsparameter sowie die zugehörigen mechanischen Daten der
unverstreckten und verstreckten Filamentgarne sind in Tabelle 1 zusammengefasst. Darin
sind den Daten für die mechanischen Eigenschaften, der nach den verschiedenen Verfahren
hergestellten Filamentgarne, die Ergebnisse für ein nach dem gleichen Verfahren hergestelltes
Referenzfilamentgarn ohne Wasserstoffperoxidapplikation vorangestellt. Im Falle des
LOY- und des POY-Prozesses sind neben den Werten der Spinnspulen auch die Werte der
nachverstreckten Filamentgarne angegeben, so wie sie durch einen separaten Verstreckprozess
auf einer Streck-Spul-Anlage unter Einstellung einer Restdehnung von 20-30% erreicht
werden. Im Falle des FDY-Prozesses steht das voll verstreckte Filamentgarn am Ende
des Prozesses bereits zur Verfügung, d.h. die Zwischenstufe des unverstreckten Filamentgarns
kann nicht isoliert bzw. charakterisiert werden.
[0042] Im Vergleich zu den Filamentgarneigenschaften der entsprechenden Referenzfilamentgarne
zeigt sich - insbesondere für die voll versteckten Filamentgarne - , dass es durch
die Wasserstoffperoxidapplikation zu keiner Verschlechterung der garnmechanischen
Eigenschaften kommt. D.h., die stattfindende Modifizierung der Filamentoberfläche
führt nur dazu, dass eine Funktionalisierung erreicht, die dazu ausreicht deren Hydrophilie
zu verbessern und die Anfärbbarkeit der Filamentgarne wünschenswert zu verbessern.
Die verbesserte Anfärbbarkeit ist nachgerade das entscheidende Indiz für die Lehre
aus der Erfindung und ein Maß für die erreichte Modifizierung.
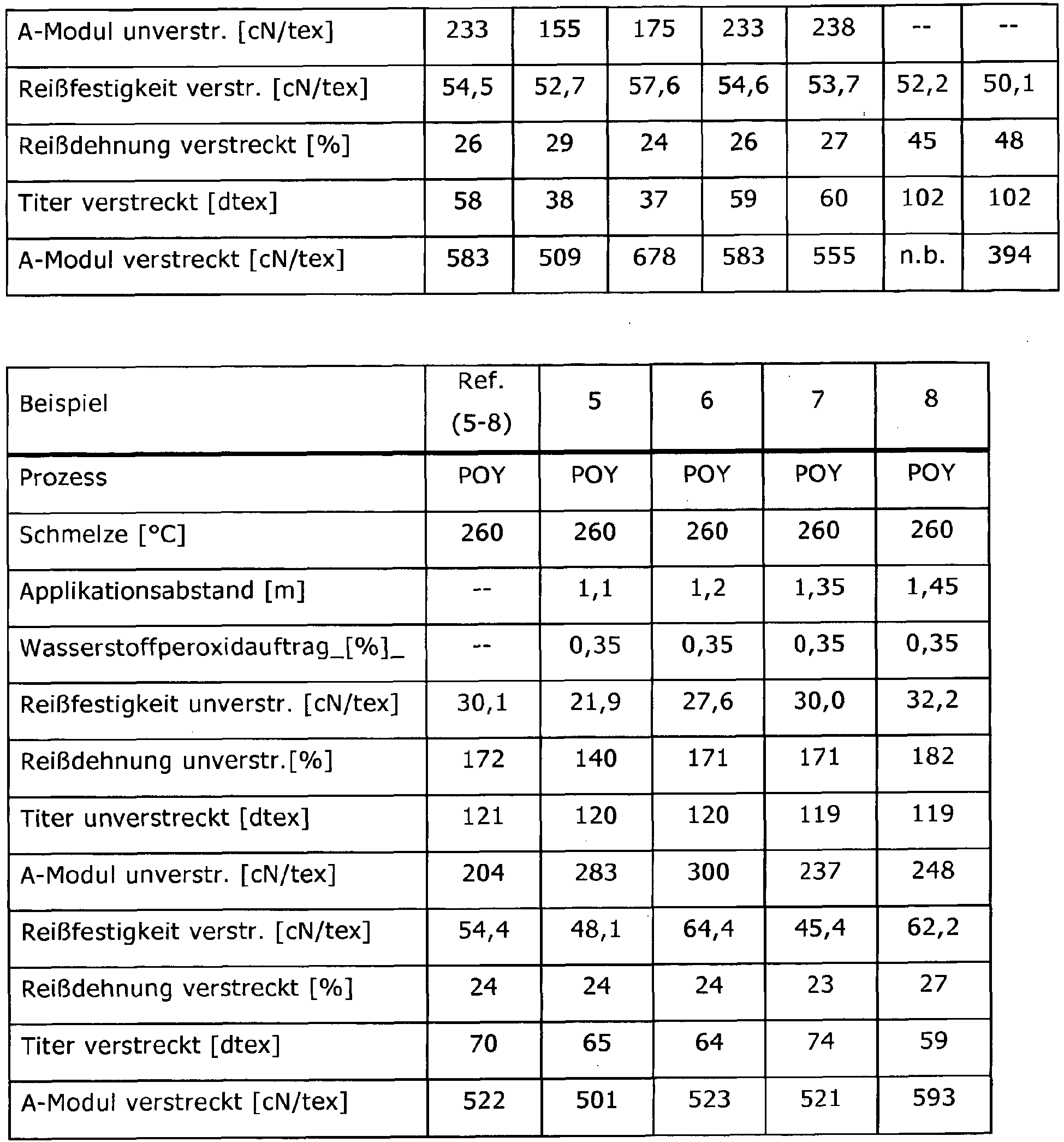
[0043] Zur praktischen Durchführung der Färbungen werden daher handelsübliche Küpensowie
Dispersionsfarbstoffe nach den Rezepturen der Hersteller eingesetzt. Im Einzelnen
werden dabei die folgenden Bedingungen angewendet, um die aus den verstreckten Filamentgarnen
hergestellten Strickstrümpfe zu färben.
[0044] Zunächst werden die Gestricke nach Herstellerangabe bei 60 °C in der Färbeapparatur
30 min gewaschen, wozu 0,5 g/l Kieralon OLB (tensidische Verbindung) (Hersteller:
BASF SE) und 0,5 g/l Soda in der Waschflotte eingesetzt werden. Danach wird dreimal
gespült, geschleudert und an der Luft getrocknet. Anschließend wird bei 120°C 30 Sekunden
in einem Dämpfer thermofixiert: die eigentliche Färbung wird als Thermosol-Färbung
ausgeführt, wobei ein Färbeflotte aus 20 g/l Farbstoff-Stamm mit 10 g/l Avolan IS
(tensidische Verbindung) (Hersteller. Bayer AG) und 10 g/l Primasol AMK (tensidische
Verbindung) (Hersteller: BASF SE) zum Einsatz kommt. Diese wird in zwei Passagen im
Foulard (Anpressdruck: 1,6 bar, Durchlaufgeschwindigkeit: 1,5 m/min) auf das Textil
aufgebracht und dieses dann 90 Sekunden bei 120°C getrocknet. Fixiert wird fünf Minuten
bei 145°C und 50% relativer Feuchte, bevor das Textil viermal bei 80°C mit Wasser
ausgewaschen und anschließend an der Luft getrocknet wird.
[0045] Für die Herstellung der jeweiligen Farbstoff-Stammflotten wurden die DispersionsFarbstoffe:
Dianix Yellow CC, Dianix Red CC und Dianix Blue CC sowie die Indanthren-Farbstoffe:
Indanthren Yellow 5GF, Indanthren Red FGL, Indanthren Navy Blue G, Indanthren Goldorange
G, Indanthren Red LGG sowie Indanthren Blue RS verwendet.
[0046] Die Beurteilung der Färbbarkeit erfolgt anhand der K/S-Werte, die mit einem handelsüblichen
Farbmessgerät aus den dort gemessenen farbmetrischen Werten ermittelt werden. Der
K/S-Wert ergibt sich aus der Formel (100-
R)
2/200R. Dabei ist R der Prozentsatz des von der gefärbten Probe reflektierten Lichts,
der bei der Wellenlänge mit maximaler Absorption gemessen wird. In der folgenden Tabelle
sind diese Werte den entsprechenden Werten einer nicht mit Wasserstoffperoxid behandelten
Probe gegenübergestellt.
Tabelle 2:
K/S-Werte |
Dianix Yellow CC |
Dianix Red CC |
Dianix Blue CC |
Indanthren Yellow 5GF |
Indanthren Red FG L |
Indanthren Blue G |
Indanthren Orange G |
Indanthren Brill. Red LGG |
Indanthren Blue RS |
ohne H2O2 |
1,62 |
2,41 |
2,39 |
0,81 |
1,02 |
0,43 |
0,66 |
0,85 |
0,85 |
mit H2O2 |
3,54 |
6,2 |
3,14 |
4,44 |
3,26 |
1,51 |
2,56 |
4,85 |
4,55 |
[0047] Erläuterung zu den Ergebnissen: Alle mit Wasserstoffperoxid behandelten Proben zeigen
eine tiefere Anfärbung (höhere Farbstoffaufnahme). Diese hängt vom Farbstofftyp und
der Farbe ab und erreicht gegenüber der Vergleichsprobe ca. 1,5 bis 5 Mal höhere Werte.
[0048] Der weitergehenden Erläuterung der Erfindung dienen die nachfolgenden Ausführungen
zu den sich anschließenden Fig. 1 und 2. Es wird dargestellt in
Fig. 1 eine Anlage zur Herstellung von LOY-, POY bzw. FOY-Filamentgarnen;
Fig. 2 eine Anlage zur Herstellung von FDY-Filamentgarnen.
[0049] In der Fig. 1 bedeuten: (1) Granulatbehälter, (2) Extruder, (3) Spinnkopf mit Pumpe
und Düse, (4) Fadenbildung, (5) Wasserstoffperoxid-Zwangsdosierung, (6) Wasserstoffperoxidapplikation,
(7) Fallschacht, (8) Galette 2, (9) Galette 1, (10) Spulkopf, (11) Spule.
[0050] Die in Fig. 1 beschriebene Anlage lässt sich bezüglich der darin stattfindenden Verfahrensabläufe
wie folgt beschreiben: Die Spinnanlage zur Herstellung von Filamentgarnen besteht
aus zwei Teilen, die sich auf unterschiedlichen baulichen Ebenen befinden. Der Extrusionsteil
(Extruder mit Peripherie und die Applikationseinrichtung) ist über den Fallschacht
mit der Wickeleinrichtung verbunden. Je nach eingestellter Spulgeschwindigkeit werden
die unterschiedlichen Prozesse realisiert: bei Spulgeschwindigkeiten bis etwa 1000
m/min der LOY-, bis etwa 4000 m/min der POY- und bei darüber liegenden Spulgeschwindigkeiten
der FOY-Prozess.
[0051] In der Fig. 2 bedeuten: (1) Granulatbehälter, (2) Extruder, (3) Spinnkopf mit Pumpe
und Düse, (4) Fadenbildung, (5) Wasserstoffperoxid-Zwangsdosierung, (6) Wasserstoffperoxidapplikation,
(7) Fallschacht, (8) Wickler (Spulkopf mit Galetten 1 +2 ), (9) Abliefergalettenduo,
(10) Verstreckeinheit mit drei heizbaren Galettenduos, (11) Abzugsgalette mit Verlegerrolle.
[0052] Die in der Fig. 2 beschriebene Anlage lässt sich bezüglich der darin stattfindenden
Verfahrensabläufe wie folgt beschreiben: Die Spinnanlage zur Herstellung von voll
verstreckten Filamentgarnen besteht wie die Spinnanlage der Fig. 1 aus zwei Teilen.
Der Extrusionsteil und die Verbindung zur Aufwickelebene sind identisch. Der vom Extruder
kommende Faden wird von der Abzugsgalette mit niedriger Geschwindigkeit (kleiner 1000
m/min) abgezogen und dann auf den folgenden Galettenduos bei aufsteigenden Geschwindigkeiten
unter Erwärmung verstreckt. Das Ablieferduo liefert den fertig verstreckten Faden
mit konstanter Geschwindigkeit an den Wickler, wie er im obigen POY/FOY-Prozess eingesetzt
wird. Die Spulgeschwindigkeit liegt im Bereich von 2000 bis 5000 m/min.
1. Verfahren zur Herstellung von aus wässrigen Färbeflotten färbbaren, oberflächenmodifizierten
Polyolefingarnen, dadurch gekennzeichnet, dass Polyolefinfilamentgarne auf Basis von Homo- und/oder Copolymerisaten von Propylen
und/oder Ethylen, gegebenenfalls mit einem oder mehreren Comonomeren, während der
Filamentgarnbildung im Schmelzspinnprozess zur Hydrophilisierung der Oberfläche unterhalb
des Schmelzpunktes der Polyolefinmaterialien mit einer Wasserstoffperoxidlösung behandelt
werden.
2. Verfahren nach Anspruch 1, dadurch gekennzeichnet, dass die Oberflächenbehandlung der Filamentgarne durch die chemische Reaktion einer wässrigen
Wasserstoffperoxidlösung mit den Polymermolekülen an der Filamentoberfläche erreicht
wird.
3. Verfahren nach Anspruch 2, dadurch gekennzeichnet, dass eine wässrige Wasserstoffperoxidlösung eingesetzt wird, deren Konzentration weniger
als 35 Gew.-%, insbesondere 0,5 bis weniger als 35 Gew.-%, beträgt.
4. Verfahren nach Anspruch 3, dadurch gekennzeichnet, dass die Konzentration der wässrigen Wasserstoffperoxidlösung 1 bis 30 Gew.-%, insbesondere
1,5 bis 10 Gew.-%, beträgt.
5. Verfahren nach einem der Ansprüche 1 bis 4, dadurch gekennzeichnet, dass die Behandlung der Oberfläche der Polyolefinfilamentgarne mit der Wasserstoffperoxidlösung
im Blasschacht der Spinneinrichtung unterhalb der Spinndüse mittels eines Präparationsstiftes
mit Zwangsdosierung durchgeführt wird.
6. Verfahren nach Anspruch 5, dadurch gekennzeichnet, dass der Applikationsabstand (zwischen Spinndüse und Applikationsstelle) der Wasserstoffperoxidlösung
im Blasschacht weniger als 4 m, insbesondere weniger als 2 m, beträgt.
7. Verfahren nach Anspruch 6, dadurch gekennzeichnet, dass der Applikationsabstand bis zu 1,5 m beträgt.
8. Verfahren nach mindestens einem der Ansprüche 2 bis 7, dadurch gekennzeichnet, dass die Menge an aufgebrachtem (reinem) Wasserstoffperoxid, bezogen auf das Filamentgarngewicht,
auf bis zu etwa 10 Gew.-%, insbesondere auf mehr als 0,1 Gew.-%, eingestellt wird.
9. Verfahren nach Anspruch 8, dadurch gekennzeichnet, dass die Menge an aufgebrachtem (reinem) Wasserstoffperoxid, bezogen auf das Filamentgarngewicht,
auf 0,2 bis 2 Gew.-% eingestellt wird.
10. Verfahren nach mindestens einem der vorhergehenden Ansprüche, dadurch gekennzeichnet, dass die Filamentgarne unter der Spinndüse mit einer Geschwindigkeit zwischen 300 und
3000 m/min, insbesondere zwischen 750 und 2700 m/min, abgezogen und danach verstreckt
und auf Spulen aufgewickelt werden.
11. Verfahren nach mindestens einem der vorhergehenden Ansprüche, dadurch gekennzeichnet, dass das Verfahren, insbesondere über dem Polymerdurchlass im vorgeschalteten Extruder,
so gesteuert wird, dass der Filamenttiter der hergestellten Filamentgarne auf 0,1
dtex bis 20 dtex eingestellt wird.
12. Verfahren nach Anspruch 11, dadurch gekennzeichnet, dass die Einstellung des Filamenttiters derartig erfolgt, dass bei der späteren Anwendung
der Filamentgarne in Teppichen der Filamenttiter zwischen 10 und 20 dtex, in Kleidungen
zwischen 1 und 5 dtex und in Textilien auf Basis von Mikrofasern weniger als etwa
1 dtex beträgt.
13. Verfahren nach mindestens einem der vorhergehenden Ansprüche, dadurch gekennzeichnet, dass das zur Filamentgarnherstellung herangezogene Homo- und/oder Copolymerisat bezüglich
einer Schmelzflussrate so eingestellt ist, dass die Fadenbildung sich wie üblich einstellt,
insbesondere im Falle von Polypropylen (PP) die Schmelzflussrate MFR [g/10 min], gemessen
nach ISO1133, bei 230°C und 2,16 kg Belastung, zwischen 1 und 600, insbesondere zwischen
10 und 45, liegt.
14. Polyolefinfilamentgarne, erhältlich gemäß einem Verfahren nach mindestens einem der
vorangegangenen Ansprüche und im Anschluss an deren Herstellung mit Küpenfarbstoffen
gefärbt, wobei die Polyolefinfilamentgarne eine Farbtiefe aufweisen, angegeben als
K/S-Wert, die mindestens doppelt so groß ist, wie der Wert, der mit einer nicht mit
Wasserstoffperoxid behandelten und gefärbten Probe erreicht wird.
15. Verwendung der Polyolefinfilamentgarne, hergestellt nach mindestens einem der Ansprüche
1 bis 13, zur Herstellung von textilen Flächengebilden, insbesondere von Gestricken,
Geweben, Vliesen und Gewirken.
16. Verwendung der textilen Flächengebilde nach Anspruch 15 zum anschließenden Färben
mit Küpenfarbstoffen.
1. A method for producing surface-modified polyolefin yarns dyeable from aqueous dye
baths, characterized in that polyolefin filament yarns based on homo- and/or copolymerizates of propylene and/or
ethylene, optionally with one or more comonomers, are treated with a hydrogen peroxide
solution for hydrophilizing the surface during the filament yarn formation in the
melt spinning process below the melting point of the polyolefin materials.
2. The method according to claim 1, characterized in that the surface treatment of the filament yarns is achieved by the chemical reaction
of an aqueous hydrogen peroxide solution with the polymer molecules on the filament
surface.
3. The method according to claim 2, characterized in that an aqueous hydrogen peroxide solution is employed, the concentration of which is
less than 35 % by wt., in particular 0.5 to less than 35 % by wt.
4. The method according to claim 3, characterized in that the concentration of the aqueous hydrogen peroxide solution is 1 to 30 % by wt.,
in particular 1.5 to 10 % by wt.
5. The method according to any one of claims 1 to 4, characterized in that the treatment of the surface of the polyolefin filament yarns with the hydrogen peroxide
solution is performed in the blow duct of the spinning device below the spinning nozzle
by means of a preparation pin with forced metering.
6. The method according to claim 5, characterized in that the application distance (between spinning nozzle and application location) of the
hydrogen peroxide solution in the blow duct is less than 4 m, in particular less than
2 m.
7. The method according to claim 6, characterized in that the application distance is up to 1.5 m.
8. The method according to at least one of claims 2 to 7, characterized in that the amount of applied (pure) hydrogen peroxide related to the filament yarn weight
is adjusted to up to about 10 % by wt., in particular to more than 0.1 % by wt.
9. The method according to claim 8, characterized in that the amount of applied (pure) hydrogen peroxide related to the filament yarn weight
is adjusted to 0.2 to 2 % by wt.
10. The method according to at least one of the preceding claims, characterized in that the filament yarns are withdrawn below the spinning nozzle with a speed between 300
and 3000 m/min, in particular between 750 and 2700 m/min, and thereafter stretched
and wound to reels.
11. The method according to at least one of the preceding claims, characterized in that the method, in particular above the polymer passage in the preceding extruder, is
controlled such that the filament titer of the produced filament yarns is adjusted
to 0.1 dtex to 20 dtex.
12. The method according to claim 11, characterized in that the adjustment of the filament titer is effected such that in the subsequent application
of the filament yarns in carpets, the filament titer is between 10 and 20 dtex, in
clothes between 1 and 5 dtex and in textiles based on microfibers less than about
1 dtex.
13. The method according to at least one of the preceding claims, characterized in that the homo- and/or copolymerizate used for filament yarn production is adjusted with
respect to a melt flow rate such that the thread formation appears as usual, in particular
in the case of polypropylene (PP), the melt flow rate MFR [g/10 min] measured according
to ISO 1133, at 230 °C and 2.16 kg of load is between 1 and 600, in particular between
10 and 45.
14. Polyolefin filament yarns obtainable according to a method according to at least one
of the preceding claims and dyed with vat dyes subsequent to the production thereof,
wherein the polyolefin filament yarns have a color depth, indicated as a K/S value,
which is at least twice as large as the value, which is achieved with a sample not
treated with hydrogen peroxide and dyed.
15. A use of the polyolefin filament yarns produced according to at least one of claims
1 to 13 for producing textile fabrics, in particular knitted fabrics, woven fabrics,
non-woven fabrics and crocheted fabrics.
16. The use of the textile fabrics according to claim 15 for subsequent dying with vat
dyes.
1. Procédé de fabrication de filés de polyoléfine modifiés en surface, aptes à la teinture
dans des bains de teinture aqueux, caractérisé en ce que des fils continus de polyoléfine à base d'homo- et/ou de copolymères de propylène
et/ou d'éthylène, éventuellement avec un ou plusieurs comonomères, sont traités avec
une solution de peroxyde d'hydrogène pendant la formation des fils continus dans le
procédé de filage direct pour hydrophiliser la surface, en-dessous du point de fusion
des matériaux de polyoléfine.
2. Procédé selon la revendication 1, caractérisé en ce que le traitement superficiel des fils continus est réalisé par la réaction chimique
d'une solution aqueuse de peroxyde d'hydrogène avec les molécules polymères sur la
surface des filaments.
3. Procédé selon la revendication 2, caractérisé en ce qu'on utilise une solution aqueuse de peroxyde d'hydrogène dont la concentration est
inférieure à 35 % en poids, en particulier de 0,5 à moins de 35 % en poids.
4. Procédé selon la revendication 3, caractérisé en ce que la concentration de la solution aqueuse de peroxyde d'hydrogène est de 1 à 30 % en
poids, en particulier de 1,5 à 10 % en poids.
5. Procédé selon l'une des revendications 1 à 4, caractérisé en ce que le traitement de la surface des fils continus de polyoléfine avec la solution de
peroxyde d'hydrogène est réalisé dans le tube d'injection d'air du dispositif de filage
endessous de la buse de filage à l'aide d'une broche de préparation avec dosage forcé.
6. Procédé selon la revendication 5, caractérisé en ce que la distance d'application (entre la buse de filage et le point d'application) de
la solution de peroxyde d'hydrogène dans le tube d'injection d'air est inférieure
à 4 m, en particulier inférieure à 2 m.
7. Procédé selon la revendication 6, caractérisé en ce que la distance d'application peut aller jusqu'à 1,5 m.
8. Procédé selon au moins l'une des revendications 2 à 7, caractérisé en ce que la quantité de peroxyde d'hydrogène (pur) appliquée est, par rapport au poids du
fil continu, ajustée à une valeur allant jusqu'à environ 10 % en poids, en particulier
supérieure à 0,1 % en poids.
9. Procédé selon la revendication 8, caractérisé en ce que la quantité du peroxyde d'hydrogène (pur) appliquée est, par rapport au poids du
fil continu, ajustée à une valeur de 0,2 à 2 % en poids.
10. Procédé selon au moins l'une des revendications précédentes, caractérisé en ce que les fils continus sont, en-dessous de la buse de filage, déroulés à une vitesse comprise
entre 300 et 3000 m/min, en particulier entre 750 et 2700 m/min, puis étirés et enroulés
sur des bobines.
11. Procédé selon au moins l'une des revendications précédentes, caractérisé en ce que le procédé est, notamment par l'intermédiaire du passage de polymère dans l'extrudeuse
montée en amont, piloté de telle sorte que le titre filamentaire des fils continus
fabriqués soit ajusté à une valeur de 0,1 dtex à 20 dtex.
12. Procédé selon la revendication 11, caractérisé en ce que l'ajustement du titre filamentaire est réalisé par le fait que, lors de l'utilisation
ultérieure des fils continus, le titre filamentaire soit compris dans des tapis entre
10 et 20 dtex, dans des vêtements entre 1 et 5 dtex et dans des textiles à base de
microfibres inférieur à environ 1 dtex.
13. Procédé selon au moins l'une des revendications précédentes, caractérisé en ce que l'homo- et/ou le copolymère utilisé pour la fabrication des fils continus est, pour
ce qui est de son indice de fluidité, ajusté de telle sorte que la formation des fils
soit ajustée comme d'habitude, et qu'en particulier dans le cas du propylène (PP)
l'indice de fluidité MFR (g/10 min), mesuré selon ISO 1133 à 230°C sous une charge
de 2,16 kg, soit compris entre 1 et 600, en particulier entre 10 et 45.
14. Fils continus de polyoléfine, pouvant être obtenus par un procédé selon au moins l'une
des revendications précédentes, et colorés par des colorants de cuve après leur fabrication,
les fils continus de polyoléfine présentant une profondeur de couleur, exprimée par
la valeur K/S, qui est au moins deux fois plus grande que la valeur qui est atteinte
avec un échantillon teint et qui n'a pas été traité au peroxyde d'hydrogène.
15. Utilisation des fils continus de polyoléfine fabriqués selon au moins l'une des revendications
1 à 13 pour la fabrication de structures textiles bidimensionnelles, en particulier
de tricots, de tissus, de non-tissés et d'articles de bonneterie.
16. Utilisation des structures textiles bidimensionnelles selon la revendication 15 pour
la teinture, effectuée ensuite, avec des colorants de cuve.