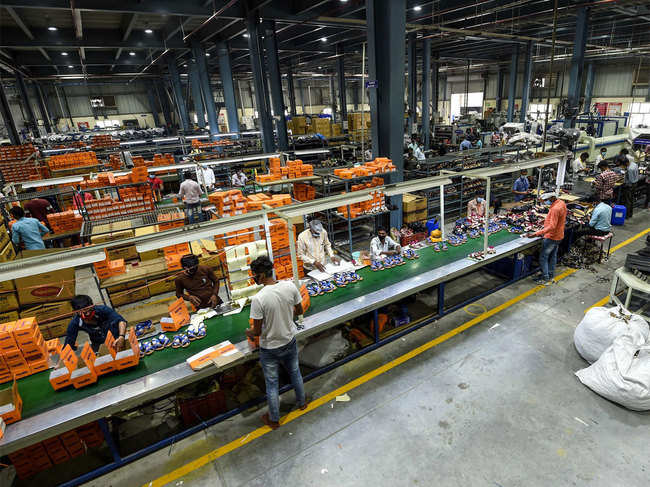

In his seminal 2005 book, “The World is Flat”, Thomas Friedman convincingly argued that the barriers to globalisation had disappeared and that the world was collectively entering a phase of extraordinary economic efficiency. Goods would be produced where they could be made most cheaply and then shipped all over the world, often just in time for consumption. The concurrent liberal political climate was a key factor in the growing volume of cross border movement of money, goods, education and tourism.
This phenomenon of globalisation ushered in the era of export oriented manufacturing hubs, where certain countries quickly became centres of entire global market supply chains. Factories grew to phenomenal sizes, catering to global markets of cars, pasta and windows, etc. These manufacturing units also became increasingly nimble to the shifting balance of demand and supply economics, with production lines that could quickly shift from one product to another. Business investment was based on chasing efficiency and capital investments were made for the long term.
Fast forward to 2020, and the spectre of the pandemic is unravelling a considerable number of those long term assumptions. Borders are no longer open, and the political climate, fuelled by rampant inequality, is shifting to fulfilling nationalist goals of economic independence. India’s manufacturing economy has been hit with the shock of rapidly diminishing (and possibly disappearing) overseas demand. Within this gloomy context, it is plausible that manufacturing in India will reposition itself to cater to local demand. How are these factories going to produce goods in the foreseeable future?
Design matters
As with private homes, the first line of defence is preventing the virus from making an entry into the facility in question. This means allocating significant areas for thermal screening at entry points, much like the baggage screening we have become accustomed to in public places. This process will likely be automated and might look like tunnels that simultaneously disinfect, while detecting temperature. Holding areas for those with suspected infection may also need to be designed as separate structures. These will mean that transitioning into factories may take longer and work hours have to be restructured accordingly.
The design of common facilities such as toilets and cafeterias will also need urgent transformation. Light switches will give way to sensor driven occupancy based lighting. Contactless basin taps, urinal flushes and dryers are already mainstream products, but their acceptance has been low due to the higher cost of procurement. These will most likely become standard design features. Even foot operated door handles (foodles) will replace the conventional handles in such commonly shared spaces.
Factories are no longer going to rely on overtly human processes that constantly require proximity. For instance, it was not uncommon to position successive sewing machines on a garment production line at every 1.2 m (about 4 feet). Similarly, furniture assembly would see several workers working simultaneously to upholster a piece. The finishing line, where a product moves along a predetermined path and workers often repeat one small task might become more cost effective even for smaller setups.
In India, due to climatic extremes in most parts of the country, factories have traditionally relied on a mix of air cooling and air conditioning for human comfort. Going forward, the focus on air cooling is likely to increase for multiple reasons. Air cooling does not necessitate recirculation - it works on flow. Combined with passive strategies for mitigating heat through the building envelope (such as shading, double facades and insulation), it can create human comfort levels within the building even when outside temperatures become unbearable. Even humidity can be controlled more effectively through air flow when paired with porous facade design. The issue of airborne dust, detrimental to most manufacturing, will need to be tackled by forced extraction or operable facades depending on the context.
New systems
Within air-conditioned spaces, the issues of creating a sanitised environment are much more complex. No known air conditioning filtration system can inhibit the flow of a virus travelling through the air. HEPA filters typically trap objects at 2microns (sufficient for dust, pollen and mold), but most viruses will pass right through the filter. Ozone based electronic filters may be effective against viruses, but the concentrations of ozone needed to kill viruses passing through at high speed would anywhere between 5x and 10x of that allowable by public health standards.
UV lights are similarly effective on static surfaces, but are unlikely to work within an HVAC system that is circulating air. Custom air scrubbers may offer the greatest potential to sanitise air conditioned environments, but they only work effectively within smaller areas and can become significantly expensive as air volumes increase. It must be said that none of these systems have been tested for Covid-19 in particular till date and the best way to protect the air-conditioned environments is going to be by preventing its entry into the space.
An increased input cost is very likely to emerge across the board for industrial production. Whether by buyer compliance or by governmental regulation, it is unlikely that even the fringes of manufacturing will be exempt from the added expense of creating sanitised and hygienic work environments. As before, economies of scale will continue to influence profitability and smaller factories may get subsumed and acquired as the incremental cost of sanitisation will influence competitive advantage.
I4, or Industry 4.0 has been widely touted as the next generation of manufacturing. Conceived in Germany in 2011, it encompassed the widespread digitisation of production, allowing decisions to be made autonomously by machines based on sensory input from multiple sources. Integration of technology has been at the core of this development, and the pandemic is likely to spur this into the mainstream. As we begin to count the human cost of the Coronavirus, we may need to rely increasingly on machines to protect ourselves.
(The writer is Design Principal, Amit Khanna Design Associates)