Entwicklungszeit verkürzen: Schneller zum fertigen Produkt
Anbieter zum Thema
Wie können digitale Produkte und Planungsprozesse genutzt werden, um eine möglichst hohe Effizienz zu erreichen? Anhand eines Projekts aus der chemischen Industrie zeigt VTU, wie der digitale Zwilling einer Prozessanlage erstellt und so die Entwicklungszeit des Gesamtprojekts deutlich verringert werden konnte.
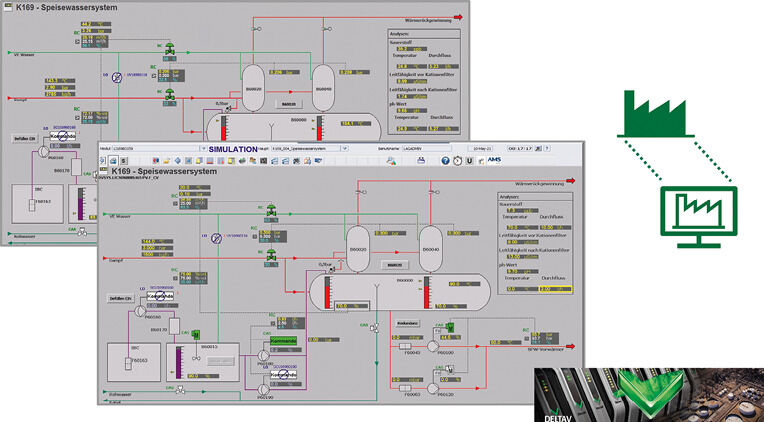
In dem Projekt war VTU für die EIC-Planung verantwortlich. Anlagen werden heute meist durch Prozessleitsysteme gesteuert, die viele Vorteile wie eine erhöhte Effizienz und reduzierte Ausfallzeiten bieten. Hier wurde das Prozessleitsystem mit einem digitalen Zwilling kombiniert, um die Entwicklungszeit bis zum Produktionsstart zu verkürzen. Das System interagierte aber nicht nur mit dem physischen Prozess in der Anlage, sondern auch mit einem digitalen Zwilling des Prozesses – und dies zu einem Zeitpunkt, als die physische Anlage noch nicht existierte beziehungsweise sich noch im Bau befand.
Neue Verwendungsmöglichkeiten für bestehende Daten
Möglich gemacht wurde dies durch die Daten, die in Engineering-Projekten anfallen und neue Verwendungsmöglichkeiten eröffnen. Dazu zählen etwa 3D-Pläne, Stücklisten oder Stellenlisten von Concept- bis hin zu Detail-Engineering – eine gute Basis zur effizienten Erstellung eines digitalen Zwillings einer Prozessanlage.
Im Sinne des Integrated Engineerings, das von dem Unternehmen seit einigen Jahren umgesetzt wird, standen alle digitalen Pläne, die während der Prozessplanung entstehen, in einem Common Data Environment (CDE) zur Verfügung. Im Rahmen des Projekts wurde eine Kombination aus Automatisierung und Simulation eingesetzt: Das Team führte das Engineering mehrheitlich in Comos durch, mit Aufgaben wie etwa Alarmschwellendefinition und Zuordnung von IOs, was zur Definition des gesamten Systems führte. Vorteilhaft war, dass in Comos verschiedene Disziplinen in einem gemeinsamen Datenbestand arbeiten, von der Verfahrenstechnik, dem P&ID, dem E&IC-Engineering bis hin zur Softwareentwicklung. Für die Automation kam Distributed Control System (DCS) DeltaV zur Verwendung, der darauf aufsetzende digitale Anlagenzwilling wurde in Mimic erstellt.
Kürzere Entwicklungszeit: Common Data Environment als Basis
Die Konsistenz der Daten ist wichtig: Zur Vermeidung von Doppelspurigkeit wurde der Datenaustausch zwischen allen Systemen weitgehend automatisiert. Comos und DCS kommunizierten über eine eigens erstellte Schnittstelle, zwischen DCS und Mimic wurde eine native Schnittstelle eingerichtet. So konnte das angepeilte Common Data Environment entstehen.
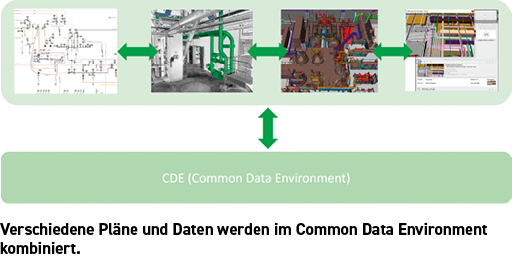
Dank dieses „Single Point of Truth“ wurden alle Planungsdaten aus Comos und DCS in Mimic übernommen, was eine automatische Erstellung des digitalen Zwillings erlaubte. Einzig die mathematischen Modelle mussten in Mimic hinzugefügt werden.
Die automatisierte Erstellung reduzierte den Aufwand der Modellerstellung und minimierte die Fehleranfälligkeit, die durch die große Anzahl von Ein- und Ausgängen bedingt wurde. Hätte jeder dieser IOs – die leicht in die Tausende gehen –manuell erstellt werden müssen, hätte dies einen enormen Aufwand bedeutet, da zusätzlich das dynamische Modell zu erstellen gewesen wäre.
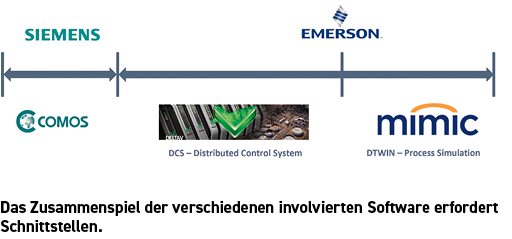
Während die Schnittstelle zwischen DeltaV und Mimic dank einer Harmonisierung zwischen den Tools trivial war, stellten der Export aus Comos und der Import in DeltaV kundenspezifische Funktionen dar, die auf einem Text-Export-Generator basierten. Dadurch konnte in Mimic die gesamte Instrumentierung mit dem generierten Aktuatormodell verwendet werden, um das dynamische Prozessmodell zu erstellen. Auf diese Weise entstand ein digitaler Zwilling auf der Grundlage aller vorhandenen Daten aus einer integrierten technischen Umgebung.
Das Ergebnis: Nach drei Wochen stand ein funktionsfähiger
digitaler Zwilling zur Verfügung, der den neu geplanten Prozess als mathematisches Modell digital abbildete und somit Monate vor dem echten Prozess existierte. Dieser konnte über das Prozessleitsystem exakt wie der echte Prozess gesteuert werden.
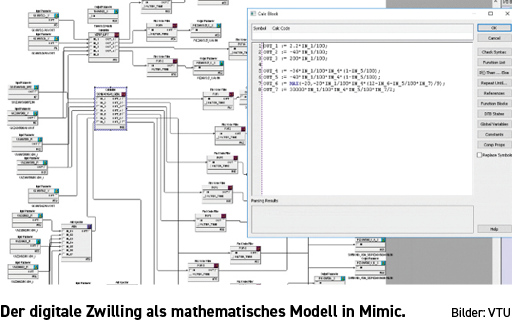
Verbesserungsmöglichkeit durch standardisiertes Datenmodell
Für die Chemie- und Pharmaindustrie wäre ein standardisiertes Modell mit herstellerübergreifenden Schnittstellen zwischen den verschiedenen Planungs-, Dokumentations- und Steuerungsdisziplinen von großem Vorteil. Dies würde den Datenfluss von der Prozessplanung mit R&I-Erstellung, dem 3D-Modell mit Gebäude- und Aufstellungsplanung zu DCS und Scada mit Anlagensteuerung, Simulation und ERP-Anbindung ermöglichen – begleitet von den ausführenden Gewerken bei Instrumentierung, Bestellung, Validation, Software und Simulation. Das Projekt funktionierte mit etwas Zusatzaufwand auch ohne standardisiertes Datenmodell. Dennoch sprechen einige Vorteile dafür:
→ Kein Erfordernis für die Implementierung der Schnittstelle zwischen Comos & DeltaV durch das Projektteam
→ Einfachere, schnellere und umfassendere Erstellung des Common Data Environment
→ Konsequenter „Single Point of Truth“ ohne Fehlerrisiko durch den Datentransfer zwischen den Systemen
Reduzierte Entwicklungszeit für Gesamtentwicklung und Inbetriebnahme
Welche Vorteile brachte der digitale Anlagenzwilling mit sich? Insgesamt konnte die Entwicklungszeit des Projekts um zehn Prozent verkürzt werden. Dank der frühen Verfügbarkeit des digitalen Zwillings wurden diverse Arbeiten vorgezogen, wie etwa Operator-Trainings, eine virtuelle Inbetriebnahme der Software sowie erste Tests anhand von Simulationen. Lange Lieferzeiten für Hardwarekomponenten konnten optimal genutzt werden. Insgesamt wurde so eine Reduktion der Inbetriebnahmezeit um 30 Prozent erreicht und 25 Prozent der gesamten User-Trainings anhand des digitalen Zwillings durchgeführt, da der Workflow frühzeitig definiert sowie Änderungen am Prozess einfach berücksichtigt werden konnten. Zum anderen ermöglichte der digitale Zwilling neben der Verkürzung der Entwicklungszeit Tests und Änderungen ohne physikalische Einflüsse: Jegliche Gefährdung der Anlagensicherheit konnte somit ausgeschlossen werden.
Nun stellt sich die Frage: Wo liegt der Unterschied zwischen dem realen System und seinem digitalen Zwilling? Aus rein optischer Sicht: Es gibt keinen. Die HMIs für ein echtes und ein simuliertes System sind die gleichen, der Anblick des DeltaV-Bildschirms gibt keine Hinweise darauf, ob es sich um ein echtes System oder einen digitalen Zwilling handelt.
Schlüsselfaktoren für digitale Zwillinge
Unterschiede wurden erst im Verhalten hinter der HMI sichtbar. Denn bei der Simulation ist die Qualität der Modellierung ausschlaggebend. Einige der wichtigsten Faktoren sind:
→ Gültigkeitsgrenzen: Es ist wichtig zu wissen, in welchem Bereich das Modell validiert ist und verwendet werden kann. Außerhalb dieser Grenzen kann das Modell instabiles Verhalten zeigen.
→ Datenqualität: Ein Modell ist nur so gut wie die Daten, auf denen es basiert.
→ Modellierungstiefe: Hier geht es um den Detailgrad des Modells – so wurde etwa auf die Modellierung des Wärmeübergangs durch die Wand eines Behälters verzichtet.
→ Simulationstechnik: Es gibt viele Simulationsmethoden, von der einfachen stationären Berechnung über ein dynamisches Modell mit pauschalen Massen unter Verwendung von Differentialgleichungen bis hin zu einer komplexen 3D-CFD-Simulation.
Der Schlüssel zu einem guten digitalen Zwilling liegt in der Qualität sowie für den beabsichtigten Zweck geeigneten Methoden und Modellen.
Die Autoren: Stefan Pauli ist Senior Data Scientist bei VTU. Mario Petschenig ist Branch Manager bei VTU.
Lesen Sie auch: Teleskopauszug für die Outdoor-Küche: Belastbar und zuverlässig