Aachener Werkzeugmaschinen-Kolloquium (AWK): Produktionstechnik für Hochlohnländer
>> Das Ende Mai stattfindende Aachener Werkzeugmaschinen Kolloquium behandelt Themen rund um die moderne Produktion in Hochlohnländern. Der Erhalt von Arbeitsplätzen in Hochlohnländern stellt die Produktionstechnik vor die Herausforderung zum weiteren Ausbau der Technologieführerschaft. Zwei Themenbereich werden in diesem Zusammenhang im folgenden Beitrag vorgestellt: Zum einen die hybride Produktionstechnik und zum anderen die Präzisionsfertigung im Bereich der Optikfertigung.
Anbieter zum Thema
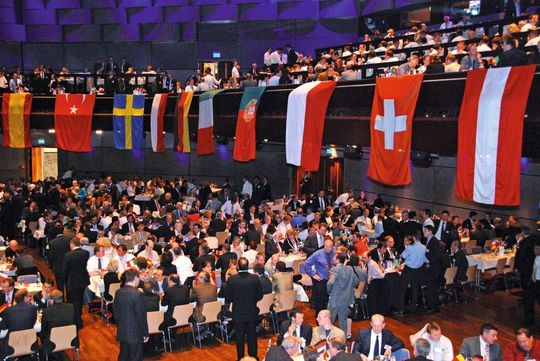
Damit die Produktionstechnik nicht aus den Hochlohnländern abwandert, muss ein hoher Mehrwert geschaffen werden, respektive der Anteil der Lohnkosten an den Gesamtkosten reduziert werden. Im Ersten Teil dieses Beitrages wird aufgezeigt, wie die hybride Produktionstechnik hierzu einen entscheidenden Beitrag leisten kann. Dank ihr ist es möglich, Bearbeitungsprozesse effizienter und Produktionsmaschinen flexibler bei gleichzeitiger Steigerung des Automatisierungsgrads zu gestalten. Im Gegenzug steigt die System- und Prozess-Komplexität, was zum Einen das Kopieren hybrider Technologien erschwert. Zum Anderen stellt insbesondere die aus der Komplexität resultierende schwierigere Beherrschbarkeit sowohl von hybriden Prozessen als auch hybriden Systemen in vielen Fällen eine Hürde für die industrielle Etablierung dar. Im darauffolgenden zweiten Teil wird aufgezeigt, welche Anforderungen Optiken an moderne Fertigungsprozesse stellen.
Teil 1: Hybride Prozesse
Der Begriff «Hybrid» wird in der Produktionstechnik sowohl prozessseitig, als auch systemseitig verwendet. Hybride Prozesse sind dadurch gekennzeichnet, dass verschiedene Mechanismen miteinander hauptzeitparallel kombiniert werden. Ziel ist es hierbei, die Nachteile von einzelnen Verfahrensmechanismen durch die Verfahrenskombination zu reduzieren oder durch eine gezielt lokale Manipulation der Werkstoffeigenschaften die Bearbeitungsprozesse effizienter zu gestalten, indem Prozesskräfte und der Werkzeugverschleiss reduziert und die Leistungsfähigkeit gesteigert werden.
Laserunterstützte Hybrid-Bearbeitung
Die laserunterstützte Hybrid-Bearbeitung kombiniert beispielsweise eine laserinduzierte Werkstoffentfestigung mit der konventionellen Bearbeitung wie der Zerspanung (Drehen, Fräsen, Bohren), dem Umformen (Drückumformen, Tiefziehen, Biegen, Prägen) oder dem spanlosen Scherschneiden.
Mit dem laserunterstützten Drehen und Fräsen können sprödharte Hochleistungskeramiken mit geometrisch bestimmter Schneide bearbeitet werden. Neueste Entwicklungen ermöglichen eine in der Frässpindel integrierte Laserstrahlführung. Hierbei wird der Laserstrahl vor der rotierenden Schneide ausgekoppelt und synchron zur Spindeldrehung gepulst, so dass ausschliesslich die Zerspanungszone vor dem Schneideneingriff bestrahlt und hierdurch entfestigt wird. Im Vergleich zu bisherigen Ansätzen des laserunterstützten Fräsens (Positionierung des Laserbrennflecks vor dem Fräswerkzeug) konnten hierbei die Prozesskräfte und der Werkzeugverschleiss bei der Bearbeitung von Inconel und Siliziumnitridkeramik signifikant reduziert werden.
Laserunterstütztes Drückumformen und Schneiden
Mit dem laserunterstützten Drückumformen wird der Umformgrad des Bauteils lokal in der Umformzone deutlich gesteigert. Das laserunterstützte Scherschneiden ist ein neues Hybrid-Verfahren, welches erstmals sowohl konventionelle Stanz-/ Nibbelmaschinen als auch Exzenterpressen dazu befähigt, im Normalschneidverfahren durchgängige Glattschnitte bei gleichzeitiger Reduktion der Schneidkräfte, des Schnittschlags und der Geräusch-Emissionen zu erzielen.
Die Überlagerung von Ultraschallschwingungen mit einem Schleifprozess ermöglicht eine Steigerung der Abtragsvolumina bei gleichzeitiger Reduzierung des Schleifscheibenverschleisses. In der industriellen Praxis konnte sich das ultraschallunterstützte Schleifen bereits zur Bearbeitung von keramischen Zahnimplantaten etablieren.
Hybride Produktionsmaschinen
Hybride Produktionsmaschinen sind dadurch gekennzeichnet, dass sie mechanische, thermische oder auch chemische Bearbeitungsverfahren in einer Maschine abbilden. So ermöglicht zum Beispiel die Kombination der konventionellen Zerspanung (Drehen, Fräsen, Bohren) mit der Lasermaterialbearbeitung (Laserhärten, Laserauftragschweissen, Laserstrukturierung) die vollautomatische Komplettbearbeitung in einer Aufspannung der Bauteile bei durchgängiger Prozessdatenkette. Durch diese Funktionalitätserweiterung von Werkzeugmaschinen wird die Fertigungsflexibilität und -tiefe insbesondere bei der Fertigung komplexer Bauteile, z.B. für den Werkzeug- und Formenbau, erhöht.
Durchlaufzeiten verkürzen
Hierdurch werden Liege-, Rüst- und Transportaufwände reduziert, so dass sich die Durchlaufzeiten verkürzen. Hybride Werkzeugmaschinen sind bereits seit vielen Jahren in der Industrie etabliert. Kombinierte Stanz-/ Nibbelmaschinen der Fa. Trumpf verfügen zum Beispiel über eine Lasersystemintegration für das maschinenintegrierte Laserstrahlschneiden.
Durch diese Multifunktionalität können insbesondere komplexe Schneidkonturen im Vergleich zum Nibbelverfahren wirtschaftlicher umgesetzt werden. Neueste Maschinenentwicklungen kombinieren die 5-Achs-Zerspanung mit dem maschinenintegrierten Laserhärten, Laserauftragschweissen oder Laserstrukturieren.
Teil 2: Moderne Optikfertigung
Funktionsintegration und Miniaturisierung stellen immer höhere Anforderungen an die eingesetzten Fertigungstechnologien. Hohe Ansprüche an Formhaltigkeit und Oberflächengüte sind insbesondere bei der Optikfertigung anzutreffen. Es werden im folgenden die Fertigung von Freiformflächen, die Funktionsintegration und die grossflächige Bearbeitung optischer Bauteile betrachtet. Dabei werden, ausgehend von anspruchsvollen Produkten, die Herausforderungen für die Fertigung abgeleitet und schliesslich die fertigungstechnischen Lösungen präsentiert.
Bedeutung photonischer Systeme
1926 wurde das Photon erstmals von G. N. Lewis als solches bezeichnet - gut 80 Jahre später gibt die «Initiative Photonik» in 2009 das Memorandum «Photonik 2020» heraus. In diesem wird die fundamentale Bedeutung photonischer Systeme und Lösungen für unsere technisierte Informationsgesellschaft aufgezeigt. Anwendungen photonischer Systeme sind dabei in allen Märkten zu finden, als Leitmärkte werden Produktion, Gesundheit, Kommunikation, Energie und Umwelt genannt. Die Einsatzgebiete reichen von sehr kleinen Stückzahlen für Spezialanwendungen, bis hin zu Massenprodukten aus dem Low-Price-Segment. Schweizer und Deutsche Firmen bedienen vor allem die High-Tech-Segmente und liefern Schlüsselkomponenten. Sei es der Teleskopspiegel für einen Satelliten oder der Spritzgusseinsatz für ein Billigprodukt, produziert in Fernost.
Schweizer und Deutsche Unternehmen stellen in vielen Bereichen der photonischen Industrie die Weltmarktführer und kämpfen bei technischen Lösungen an vorderster Front. Erwartete Wachstumsraten von 8% pro Jahr bis 2015 unterstreichen dies eindrucksvoll.
Fertigung optischer Freiformflächen
Als wichtigste Herausforderungen für die Präzisionsfertigung wurden von dem Expertengremium daher optische Anwendungen ausgewählt. Die Fertigung optischer Freiformflächen, die grossflächige Herstellung optischer Flächen und die Funktionsintegration in einem Bauteil, unter Einhaltung gesteigerter Toleranzen, werden dabei betrachtet. Die Fertigung von Freiformflächen mit optischen Oberflächen und Formtoleranzen im einstelligen Mikrometerbereich bringen die Maschinen und insbesondere die Steuerungstechnik und Software an ihre Grenzen.
Auflösungsgrenzen von CAD-CAM-Modulen
Werden solche Flächen mit hochgenauen Diamantfräsern gefräst, so sind während des Schlichtschnittes geringste Bahnabstände notwendig, um die Formhaltigkeit zu gewährleisten. Diese bringen konventionelle CAD-CAM-Module an ihre Auflösungsgrenzen und manche Maschinensteuerungen an die Grenzen verarbeitbarer Programmgrössen. Zusätzlich muss die Maschinentechnik und Maschinensteuerung die präzisen Positionen anfahren können. Schwingungen und Positionierungenauigkeiten sind dabei unbedingt zu vermeiden.
Die grossflächige Herstellung planer Flächen oder von Mikrostrukturen stellen die Maschinentechnik vor die Herausforderung langer Bearbeitungszeiten. Bis über eine Woche werden die Bauteile kontinuierlich bearbeitet. Während dieser Zeit müssen äussere Einflüsse soweit wie möglich abgehalten werden. Temperaturschwankungen, extern eingebrachte
Unterschiedliche Temperaturkoeffizienten
Schwingungen und Werkzeugverschleiss sind dabei die grössten Herausforderungen. Bei Bauteilen mit Funktionsintegration kommen besondere Herausforderungen durch Materialmixe hinzu. Unterschiedliche Temperaturkoeffizienten und mechanische Eigenschaften erschweren die Bearbeitung und das Einhalten vorgeschriebener Qualitätsmerkmale. <<
(ID:25498210)