Physikalisches Schäumen Linde und Wirth betreten neue Wege beim Schäumen mit CO2
Linde und der Kunststofftechnik-Spezialist Wirth Werkzeugbau kooperieren in Sachen physikalisches Schäumen mit Kohlendioxid, das sie damit verbessern wollen, wie jetzt bekannt wurde.
Anbieter zum Thema
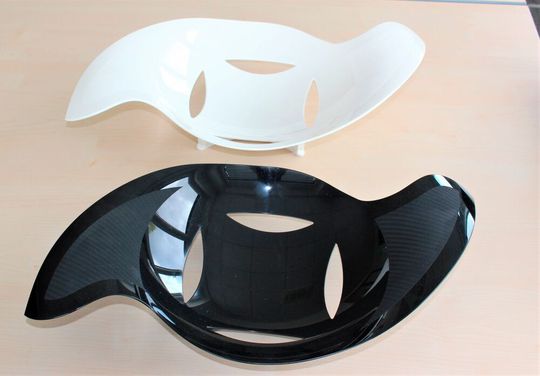
Gemeinsam erproben die beiden Unternehmen jetzt unter Praxisbedingungen Optimierungsmöglichkeiten und neue Einsatzfelder des von Linde mit Kooperationspartnern entwickelten Verfahrens „Plastinum Foam Injection Moulding“. Am 23. und 24. September werden die Ergebnisse der Kooperation übrigens im Rahmen eines Innovationstags bei Wirth im oberfränkischen Helmbrechts im großtechnischen Maßstab gezeigt. Live wird unter Einsatz des Verfahrens dann ein Ski mit geschäumtem TPU-Kern (thermoplastisches Polyurethan) im Sandwich-Spritzgussverfahren produziert.
Die Wirth Werkzeugbau GmbH mit ihren rund 70 Mitarbeitern konstruiert und fertigt auf rund 4.000 Quadratmeter Produktionsfläche Werkzeuge und Formen bis zu 40 Tonnen, für die Kunststoffverarbeitung. In diesem Bereich ist das Unternehmen mit einem eigenen Technikum ausgestattet und zudem auch verfahrenstechnisch breit aufgestellt. Ein Schwerpunkt liegt seit knapp 10 Jahren auf den Einsatzmöglichkeiten des physikalischen Schäumens. Nicht zuletzt baut Wirth heute über 50 Prozent der Werkzeuge für diesen Prozess.
Weg vom aufwendigen Stickstoffschäum-Prozess
Das bisher genutzte Verfahren basiert auf Stickstoff, hat sich auch durchaus bewährt, war aber ist insgesamt aufwendig und damit vor allem für den Einsatz mit kleineren und mittelgroßen Spritzgussmaschinen oft nicht wirtschaftlich, erklärt Wirth. Deshalb suchte man nach einer leistungsfähigeren Alternative, auf dem Stand der heutigen technischen Möglichkeiten. Diese sollte wirtschaftlicher, leichter umsetzbar und vor allem auch flexibler sein, denn das gesteckte Ziel war es, das Verfahren so für jede Spritzgießmaschine bieten zu können.
Fündig wurde man schließlich bei Linde. Denn unter der Dachmarke Plastinum bündelt Linde ein breites Spektrum an Verfahren, Anlagen und Services für gasunterstützte Prozesse, mit Blick auf die Kunststoff verarbeitende Industrie. Das Besondere daran ist, dass damit Zykluszeiten signifikant reduziert werden können und die Qualität der Bauteile deutlich besser wird. Insbesondere der Einsatz des Gases CO2 bietet bei Herstellungsverfahren wie etwa der Gasinnendrucktechnik (GID), dem Schäumen und dem Spot Cooling an Spritzgusswerkzeugen erhebliche Chancen zur Effizienzsteigerungen. Als besonders passend habe sich das Schäumverfahren „Plastinum Foam Injection Moulding“, das eben Kohlendioxid nutzt, herauskristallisiert.
Das steckt hinter dem Begriff „Plastinum Foam Injection Moulding“
Beim „Plastinum Foam Injection Moulding“ wird vorgetrocknetes Kunststoffgranulat bereits vor der Zuführung in die Spritzgießmaschine unter Druck mit CO2 beladen, erklären die Protagonisten. Das Gas diffundiert aufgrund der Wirkung des Drucks in das Granulat (Das ist etwa wie bei Mineralwasser, dem man die Kohlensäure unter Druck beigibt, das Gas aber erst bemerkt, wenn man die Flasche öffnet). Damit vereine das Verfahren die einfache Handhabung chemischer Schäumprozesse mit den positiven Effekten des physikalischen Schäumens. Das spart Material und kommt deshalb dem Leichtbau zugute, der als ein Schlüssel zur Ressourcenschonung gilt.
Darüber hinaus steigert das Verfahren die Produktqualität, indem es eine hohe dimensionale Stabilität und Funktionalität der geschäumten Spritzgussteile erreicht, sagt Wirth. Verzug und Einfallstellen werden auch minimiert. Insbesondere lassen sich auch scherempfindliche Kunststoffe wie etwa langfaserverstärkte Thermoplaste (LFT-Granulate) hervorragend verarbeiten, weil die Glasfasern nicht beschädigt werden. Auch bei geringen Wanddicken sind gute Schäumergebnisse zu erwarten. Kürzere Zykluszeiten und weniger Energieeinsatz kommen noch dazu. Weil man dabei viel mehr Gas ins Kunststoffmaterial einbringen kann, sind höhere Gewichts- und Materialreduzierungen erreichbar, als bei alternativen physikalischen Schäumverfahren oder beim chemischen Schäumen. Die höhere Gasbeladung wirke sich in diesem Sinn auch bei Polymeren wie etwa TPU oder PC (Polycarbonat) positiv aus.
Jetzt klappt die Zwischenlagerung des gasbeladenen Granulats
Ein zentrales Element ist die Fertigungszelle Plastinum Perfoamer des Systempartners Protec Polymer Processing GmbH. Sie beschleunige den Prozess und mache ihn flexibler, weil sich das gesamte erforderliche Prozessequipment per Plug&Play herstellerunabhängig mit jeder Maschine am Markt kombinieren ließe. Problemlos sei es deshalb in vorhandene Spritzgussanlagen integrierbar. In der aktuellen Version umfasst die Zelle auch einen druckbeaufschlagten Pufferbehälter. Dieser erlaubt die Zwischenlagerung des gasbeladenen Granulats und verhindert so, dass das CO2 ausdiffundiert. Dadurch ist über den gesamten Prozess eine gleichbleibend hohe Produktqualität sichergestellt, erklären die Beteiligten.
Nicht zuletzt spart „Plastinum Foam Injection Moulding“ erhebliche Kosten ein. Denn dazu nötige Maschinen können kleiner ausgelegt werden und sowohl zum Schäumen als auch für den normalen Spritzguss eingesetzt werden. Auch können mehrere Spritzgießmaschinen gleichzeitig mit Granulat versorgt werden. Im Vergleich zu herkömmlichen physikalischen Schäumverfahren lassen sich die Investitionskosten so um bis zu 60 Prozent drücken und die Schäumkosten pro Bauteil signifikant senken, heißt es weiter.
Noch mehr Partner für ambitionierte Schäumziele
Im Zuge der aktuellen Kooperation stellt Linde dem Partner Wirth einen Plastinum Perfoamer der neuesten Generation zur Verfügung. Zusammen mit dem Kunststoff-Institut Lüdenscheid (KIMW) und Protec als weiteren Entwicklungspartnern werden das Gerät und das Verfahren seitdem unter Labor- wie unter Praxisbedingungen getestet. Dafür stehen bei Wirth Spritzgussmaschinen mit 400 bis 1.300 Tonnen Schließkraft für Schussgewichte von 250 bis 5000 Gramm zur Verfügung. Versuche mit geringeren Schussgewichten werden auf kleineren Maschinen im Technikum des Kunststoff-Instituts Lüdenscheid durchgeführt, kann man erfahren. Im Ergebnis zeigt sich schon jetzt, dass „Plastinum Foam Injection Moulding“ faktisch eine überzeugende Alternative zu herkömmlichen physikalischen Schaumverfahren darstellt.
Ein Ziel dieser Zusammenarbeit ist die Weiterentwicklung des Schäumverfahrens zu einem schlüssigen Gesamtkonzept. Im Fokus stehen dabei die optimale Nutzung der Technologie und die Gestaltung der geeigneten Werkzeugtechnik sowie der Temperierung, um ideale Schäumergebnisse und bei Bedarf perfekte Oberflächen zu erzielen. Darüber hinaus präsentiert sich Wirth mit dem neuen Verfahren seinen Kunden gegenüber als innovativer Partner. Linde wiederum kann durch die Kooperation seine Kapazitäten für Kundenversuche im süddeutschen Raum erweitern.
Der Einsatz des Verfahrens ist insbesondere für Polymerverarbeiter mit kleinen- bis mittelgroßen Spritzgießmaschinen interessant, die das Verfahren flexibel und ohne hohen Invest in ihrer Produktion einsetzen wollen. Unter anderem in den Branchen Unterhaltungselektronik, Medizingeräte, Automotive und Konsumgüter sehen die Experten von Linde und Wirth viele Einsatzpotenziale. Erste Kundenprojekte wurden übrigens bereits in unterschiedlichen Industriesegmenten realisiert.
(ID:47569744)