Elektrische Eigenschaften (Durchschlagsfestigkeit) von Eloxalschichten
Roman Fuchs
Anodische Oxidschichten auf Aluminium sind keramischer Natur und in der Regel Isolatoren. Die elektrische Durchschlagsfestigkeit hängt von verschiedenen Parametern wie beispielsweise der Schichtdicke, der Legierung, den Anodisationsbedingungen, der Verdichtung (Sealing) und der Temperatur ab. Besonders der Einfluss der Temperatur darf bei elektrischen Komponenten nicht vernachlässigt werden. Schon bei Temperaturen ab 80 °C reduziert sich die elektrische Durchschlagsfestigkeit um mehr als die Hälfte! Durch spezielle Sealing-Verfahren mit AAACOAT – einer im Sol-Gel-Verfahren hergestellten anorganischen Imprägnierbeschichtung – kann die isolierende Eigenschaft nachhaltig stabilisiert werden.
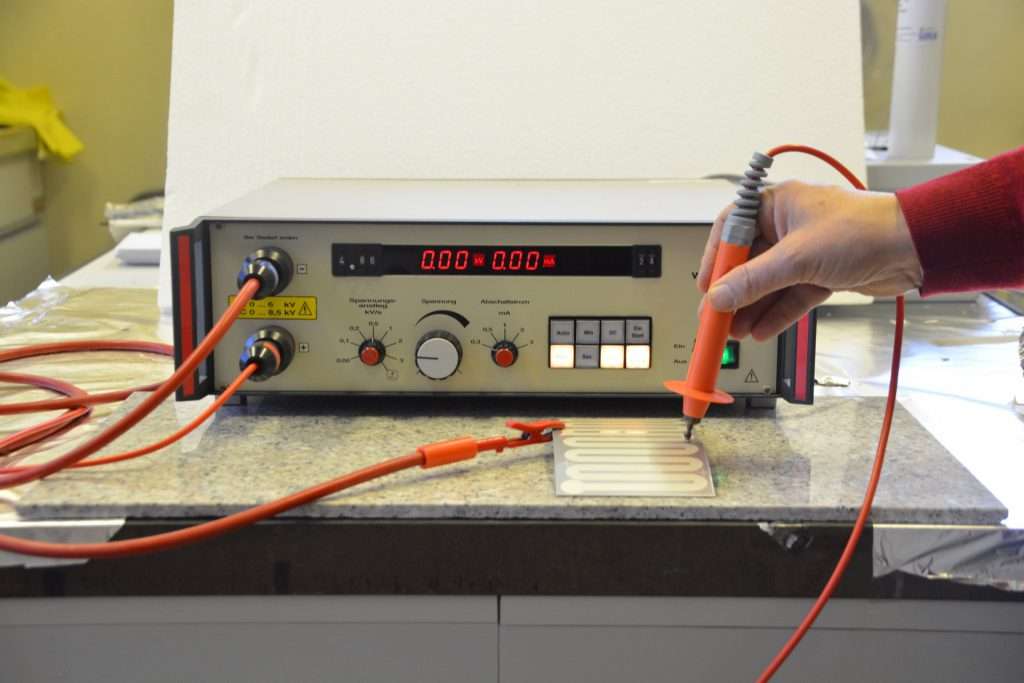
Bild 3: Elektrisches Durchschlagsmessgerät WGT-50-3. Technische Daten und typische Messparameter: Spannung 0 bis 6000 V, Spannungsanstieg 50V/s, 100V/s, Durchschlagsstrom 0,3 mA, Polung AC oder DC.
Anodische Oxidschichten auf Aluminium (Eloxal) werden wegen ihrer elektrisch isolierenden und verschleissfesten Eigenschaften oft auf Profilen, Platten, Kühlern für leistungselektronische Bauteile und Schmiedeteilen aufgebracht und zum Beispiel als Gehäuse von elektrischen Vorrichtungen wie Schaltschränken, Akkus, Transformatoren usw. verwendet. Die hohe Temperaturbeständigkeit der Eloxalschicht (bis 500 °C) wird öfters als Argument für den Einsatz dieser Oberflächenbehandlung anstelle von organischen Lackschichten usw. ins Feld geführt [1]. Es ist bekannt, dass die elektrische (Ionen-)Leitfähigkeit von keramischen Werkstoffen – und somit auch derjenigen von anodischen Oxidschichten – mit steigender Temperatur zunimmt. Hingegen ist der dramatische Abfall der elektrischen Durchschlagsfestigkeit schon bei leicht erhöhter Temperatur bei vielen Anwendern nicht geläufig (Bild 1). Es besteht somit die Gefahr, dass sicherheitsrelevante Vorschriften nicht mehr eingehalten werden.
Der Eloxalprozess
Die Eloxierung von Aluminium (Eloxal = Elektrolytische Oxidation von Aluminium) wandelt die metallische Oberfläche mit Hilfe des elektrischen Stromes in eine nichtleitende keramische Schicht um. Dabei ist das Aluminiummetall als Anode geschaltet (anodische Oxidation). Dank der porösen Struktur während des Wachstums dringt der (meistens) saure Elektrolyt in das Interface zwischen Eloxal und Aluminiummetall ein und fördert die weitere Oxidation des Metalls. So können Schichtstärken von über 100 µm erzeugt werden.
In einem weiteren Schritt werden dann die Poren durch einen Verdichtungsprozess (Sealing) geschlossen. Dies geschieht meistens einfach durch einen Quellvorgang in heissem Wasser ≥95 °C (Heisswasserverdichtung) oder durch das Befüllen der Poren mit Wachsen, organischen oder anorganischen Lacken wie zum Beispiel einem im Sol-Gel-Verfahren hergestellten Siliziumoxid. Alternativ können vor dem Verdichtungsprozess Farben in die Poren der Eloxalschicht eingebracht werden, welche der Oberfläche ein ästhetisches und dekoratives Aussehen verleihen.
Die Eloxalschicht ist als keramische Schicht äusserst hart und verschleissfest. Sie schützt das Metall vor mechanischen, chemischen und anderen Umwelteinflüssen.
Messung der elektrischen Durchschlagsfestigkeit
Die elektrische Durchschlagsfestigkeit wird bei eloxierten Aliminium-Oberflächen gemäss EN ISO 2376 [2] und bei andern Beschichtungen in Anlehnung an diese Norm durchgeführt. Zwischen dem Aluminium-Grundmetall und der Eloxaloberfläche wird eine steigende Spannung (AC/DC) angelegt, bis ein definierter Strom, der so genannte Abschaltstrom, fliesst. Diese Spannung, die unmittelbar vor dem Abschaltstrom erreicht wurde, wird abgelesen.
Die Messung wird meistens mit einem zuerst langsam ansteigenden Strom (Ionenleitung) begleitet, der dann vor dem eigentlichen elektrischen Durchschlag exponentiell ansteigt und in einem gut hörbaren Knall und – bei höheren Schichtstärken – einer Funkenentladung mündet.
Einflussfaktoren auf die elektrische Durchschlagsfestigkeit
Die Schichtdicke widerspiegelt bei dünnen Eloxalschichten (0 bis 20 µm) einen nahezu linearen Verlauf, der mit steigender Schichtdicke abflacht (Bild 4). Verdichtete Oberflächen zeigen in der Regel einen höheren Wert (Bild 4 und 5). Insbesondere eine Sol-Gel-Versiegelung mit AAACOAT erhöht die elektrische Durchschlagsfestigkeit (ED) beträchtlich (Bild 5). Eine zusätzliche dekorative Färbung mit organischen Farbstoffen vor dem Verdichten verändert die ED nicht sonderlich (Bild 6). Hoch legierte Werkstoffe wie zum Beispiel AlZn5.5MgCu tendieren zu einer geringeren ED bei vergleichbaren Schichtdicken – im Vergleich zu reinen Aluminiummetallen.
Einen dominierenden Einfluss auf die elektrische Durchschlagsfestigkeit übt die Temperatur aus. Wie bereits erwähnt reduziert sich die ED bei konventionell verdichteten Oberflächen schon bei etwa 85 °C um mehr als die Hälfte. Bei einem Rückgang auf die Ausgangstemperatur zeigen die elektrischen Durchschlagsfestigkeiten jedoch wieder die alten Werte (reversibles Verhalten). Auch die von der Schichtstärke und der Legierung abhängige Tendenz zur Schichtrissbildung ändert an der (trockenen) ED nichts (Bild 1).
Werden die Oberflächen noch höher erhitzt, zum Beispiel auf 190 °C, nimmt die ED von konventionell (Heisswasser-)verdichteten Eloxalschichten noch stärker ab. Nach Abkühlen der Proben auf Raumtemperatur liegen die elektrischen Durchschlagsfestigkeiten deutlich unter ihren Ausgangswerten (Bild 1 und 7) => irreversibles Verhalten.
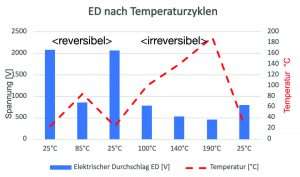
Bild 1: Elektrische Durchschlagsmessung an einer 37 µm dicken, konventionell Heisswasser-verdichteten GS-Schicht auf einer AlMg4.5Mn-Legierung (EN-AW-5083) bei verschiedenen Temperaturen. Bei Temperaturen <100 °C ist die Wärmebehandlung reversibel; über 100 °C bleibt eine irreversible Reduktion der elektrischen Durchschlagsfestigkeit.[/caption]
[caption id="attachment_103219" align="aligncenter" width="300"] Bild 2: Strom- und Spannungskurve einer typischen konventionell verdichteten Eloxalschicht (Al99.9, 26 µm). Der Stromanstieg erfolgt exponentiell bis zum elektrischen Durchschlag (ED) bei 1850V: Spannungsrampe 50V/s, Abschaltstrom 0,3 mA.
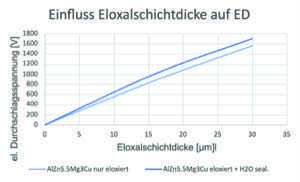
Bild 4: Linearer Anstieg der elektrischen Durchschlagsfestigkeit mit der Eloxalschicht-Dicke einer AlZn5.5Mg3Cu-Legierung (EN- AW-7022).
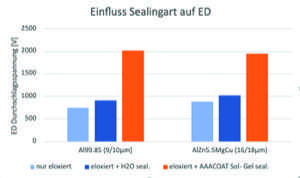
Bild 5: Die konventionell (Heisswasser-)verdichteten Oberflächen zeigen eine leicht höhere elektrische Durchschlagsfestigkeit; bei mit AAACOAT (Sol- Gel-)versiegelten Oberflächen steigt die elektrische Durchschlagsmessung deutlich an.
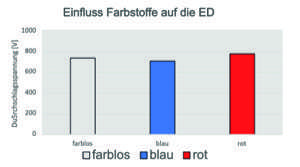
Bild 6: Eine vor dem Heisswasserverdichten eingebrachte Färbung (blau, rot) zeigt wenig Einfluss auf die elektrische Durchschlagsfestigkeit (Al99.85; 10 µm Eloxal, Spiegeloberfläche).
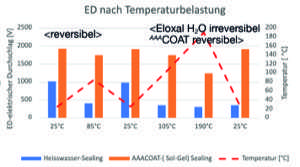
Bild 7: Vergleich des thermischen Verhaltens bei der elektrischen Durchschlagsfestigkeit einer 37 µm, konventionell Heisswasser- und einer AAACOAT/Sol-Gel verdichteten GS-Schicht auf einer AlMg4.5Mn-Legierung (EN-AW-5083). Die AAACOAT/Sol-Gel verdichtete Schicht zeigt bis 190 °C ein reversibles Verhalten!
Thermostabilisierung durch AAACOAT
Ein ganz anderes Verhalten offenbart sich bei den mit AAACOAT Sol-Gel verdichteten beziehungsweise imprägnierten Eloxaloberflächen. Hier sinkt die elektrische Durchschlagsfestigkeit bei höheren Temperaturen bis 190 °C weit weniger stark ab als bei den konventionell verdichteten Eloxalschichten. Zudem werden nach dem Rückgang der Temperatur wieder die alten Durchschlagswerte erreicht => reversibles Verhalten (Bild 7).
Diskussion der Ergebnisse
Der Grund für das reversible/irreversible Verhalten der elektrischen Durchschlagsfestigkeit bei konventionell (Heisswasser-)verdichteten GS-Eloxalschichten – je nach der jeweiligen Temperatur – ist noch nicht ganz verstanden. Es ist zwar bekannt, dass die Schichten bei erhöhter Temperatur (schon ab 50 °C) Wasser verlieren [3]. Phasenumwandlungen der amorphen Eloxalstruktur finden normalerweise aber erst bei viel höheren Temperaturen statt.
Bei der Verdichtung/Imprägnierung mit Siliziumoxid basierendem Sol-Gel (AAACOAT) tritt eine Stabilisierung ein. Aus früheren gravimetrischen Messungen wissen wir, dass das dünnflüssige niedrigviskose Sol-Gel in die Poren einzudringen vermag. Dies scheint zu einem nachhaltigen Effekt in und auf der Eloxalschicht zu führen.
Ausblick
Aufgrund der unter praxisnahen Bedingungen erhaltenen interessanten Ergebnisse streben wir weitere Untersuchungen des thermischen Verhaltens betreffend elektrische Durchschlagsfestigkeit von Eloxalschichten an. Dies erfolgt allenfalls in Zusammenarbeit mit einem Institut im Hochschulbereich.
Literatur
[1] S. Wernick, R. Pinner and P.G. Sheasby: The Surface Treatment and Finishing of Aluminium and its alloys. 1987, V2, p. 699
[2] EN ISO 2376: Anodisieren von Aluminium und Aluminiumlegierungen – Bestimmung der elektrischen Durchschlagsprüfung (ISO 2376:2010)
[3] Liliana Vera-Londono et al.: Understanding the thermal conductivity variations in nanoporous anodic aluminum oxide. Nanoscale Advances, Royal Society of Chemistry, Open Access Article, published on 17 August 2020
Dr. Roman Fuchs
FME GmbH – Fuchs Materials & Engineering
RhyTech, Bad. Bahnhofstrasse 16, 8212 Neuhausen am Rheinfall
Tel. 079 449 05 16
info@fme-gmbh.ch
www.fme-gmbh.ch
In Kürze
Die FME GmbH – Fuchs Materials & Engineering ist ein unabhängiges Unternehmen, das Beratung und Entwicklung in ausgewählten Bereichen der Material- und Beschichtungstechnik (funktionale und dekorative Oberflächen, Korrosionsschutz usw.) anbietet. Unter anderem führt es auch elektrische Durchschlagsprüfungen gemäss EN ISO 2376 oder bei andersartigen Beschichtungen in Anlehnung an diese Norm an.
Zudem entwickelt, produziert und vertreibt das Unternehmen das nanokeramische Beschichtungssystem AAACOAT, das mittels der Sol-Gel-Technologie auf Basis von Siliziumoxid selbst entwickelt wurde und besonders bei Metallen (Aluminium, Edelstahl, Kupfer/Messing) einen chemisch und mechanisch beständigen Korrosionsschutz bietet. Weitere Anwendungsgebiete dieses Systems sind Beschichtungen auf (unverdichtete) Eloxal-Oberflächen, der Passivierung und Vorbehandlung von Metallen (vor dem Lackieren) sowie auf Glas, Keramik, Emaille und temperaturresistente Kunststoffe.