



FIELD SERVICE SOLUTIONS - HYBRID EXPANSION
HYBRID EXPANSION SERVICES
Hybrid expansion is a method of expansion or re-expansion of tubes comprised of difficult materials or combination of materials. Typically situations in which the tube is harder than the tube sheet for example, a Duplex 2205 tube into a Carbon Steel alloy clad sheet. This combination proves to be particularly difficult to expand due to the metallurgical differences between the two materials and the work hardening that occurs during conventional mechanical expansion methods.
THE PROCESS
Hybrid expansion is a two step process in which two forms of expansion technology are employed to expand the tube. First a hydraulic expansion is performed. This step expands the tube and eliminates the clearance gap between the tube and tube-sheet. The second step of the process is to mechanically roll the tube using an electronic torque controlled rolling unit providing structural strength. Alternatively, the second expansion can be done using a higher pressure hydraulic expansion.
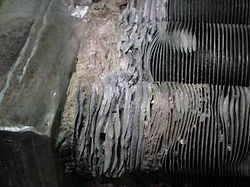
Salt buildup from leaking tubes
behind their box
Hydraulically expanding the tube first eliminates the clearance gap which allows the mechanical expansion to take place quickly with minimal work hardening and metallurgical changes to the tube as opposed to conventional rolling methods. The tube to tube-sheet joint becomes substantially stronger using these methods in conjunction with each other compared to either on its own. The hydraulic portion of the process provides an excellent seal even in holes tapered or egged by plugging or re-tubing. The mechanical stage of the process provides structural rigidity with regards to push-out strength, in addition to achieving the desired wall reduction.


THE APPLICATIONS
This process has been used effectively in a wide range of applications. Particularly in the petrochemical industry with High– Pressure fin-fan units with duplex tubes that have loosed up in service from thermal loading, shock or fretting providing a long-term solution to, what was, a difficult problem to remedy. Highlights of the process are minimum intrusion into the unit requiring just removal of the inspection port plugs and low downtime. Job completion generally takes only a day or two, depending on the number of tubes.